By Theo Harper
Abstract
By holding on to the idea of ‘origin’, understood in my research as hand-printing clay, I aim to rethink our interactions with technology and automated making. During the past three years, I have been exploring the relationship between hand-coiling clay and 3D printing clay. Hand-printing clay has always been at the origin of my work, it is a technique that has developed within my practice as a way of thinking through ideas. Hand-printing uses hand-extruded clay that, with skill, creates long hanging ropes that are pressed together. The movement is highly labored and repetitive.
Introduction
The ethical development of these technological parameters is paramount, as our entire made environment is created through interactions with computers. The stakes are environmental, geological, and political. As computers connect with making machines it is important to address issues within the automated future we are facing and have begun to live with (Bennett 2010, Vallgårda, A. (2009), Ingold, et al).
Examples include robotics and advanced manufacturing tools that rely on top-down desk-based instructions generated by a select few. This clay-first perspective on making seeks to realize a deeper understanding of the materials and processes involved in our daily lives and to describe the hybrid materiality we are part of. This approach is made possible by working with computer programmers to create disruptive innovations that affect the framework of how our fabricated environment is designed. In so doing, it is possible to ‘3D print in reverse’, allowing the digital to be touched.
In this article, I describe how 3DP clay has served as a learning tool and conduit for a new digital expansion in my practice. I describe a way of making digital sculpture that directly originates from an experienced physical place through the blended interaction with clay and new technologies. The projects that I will describe are based at Grymsdyke Farm, the European Ceramics Work Centre (EKWC) and my home studio, expressing this hybridity in the form of hand-printed, digital models, robotically printed and 3DP clay and ceramics.
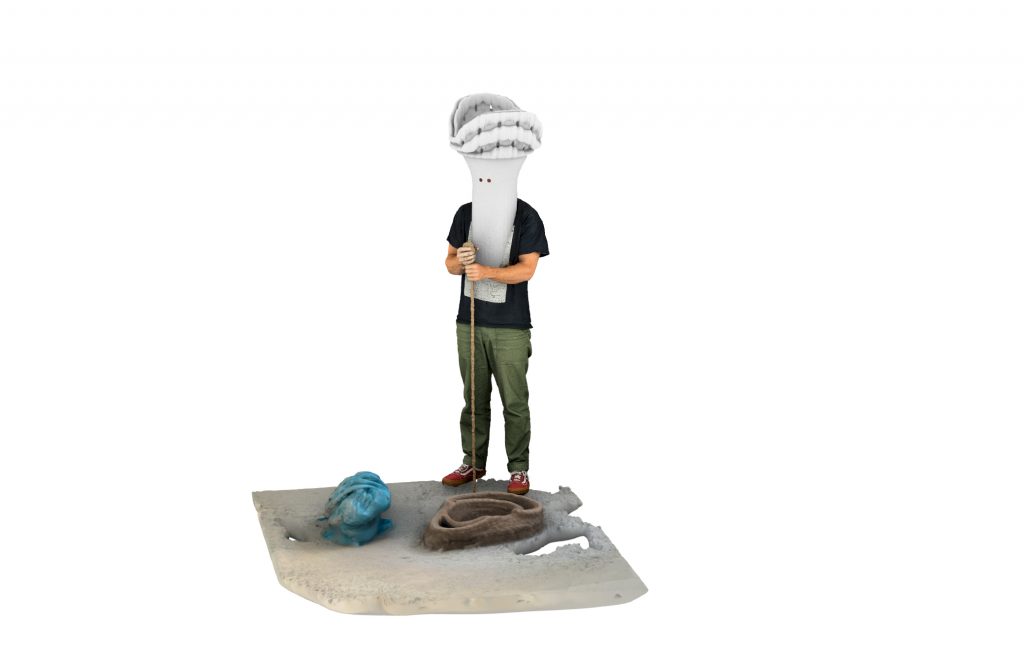
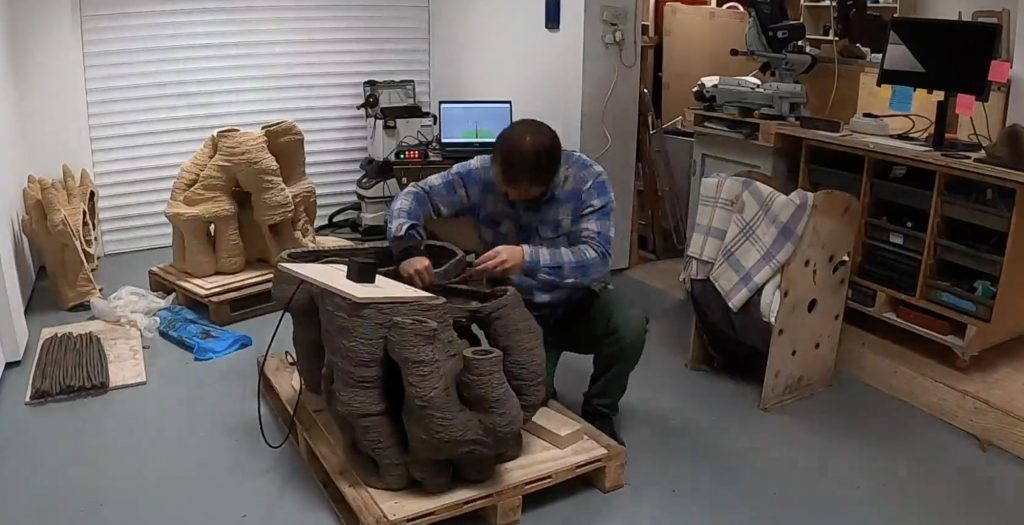
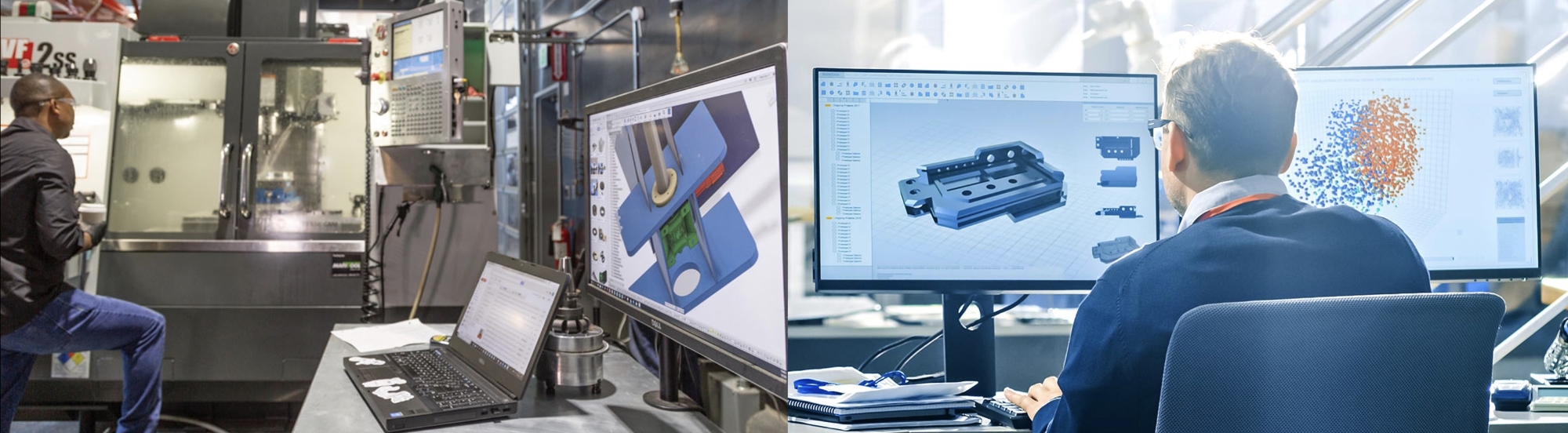
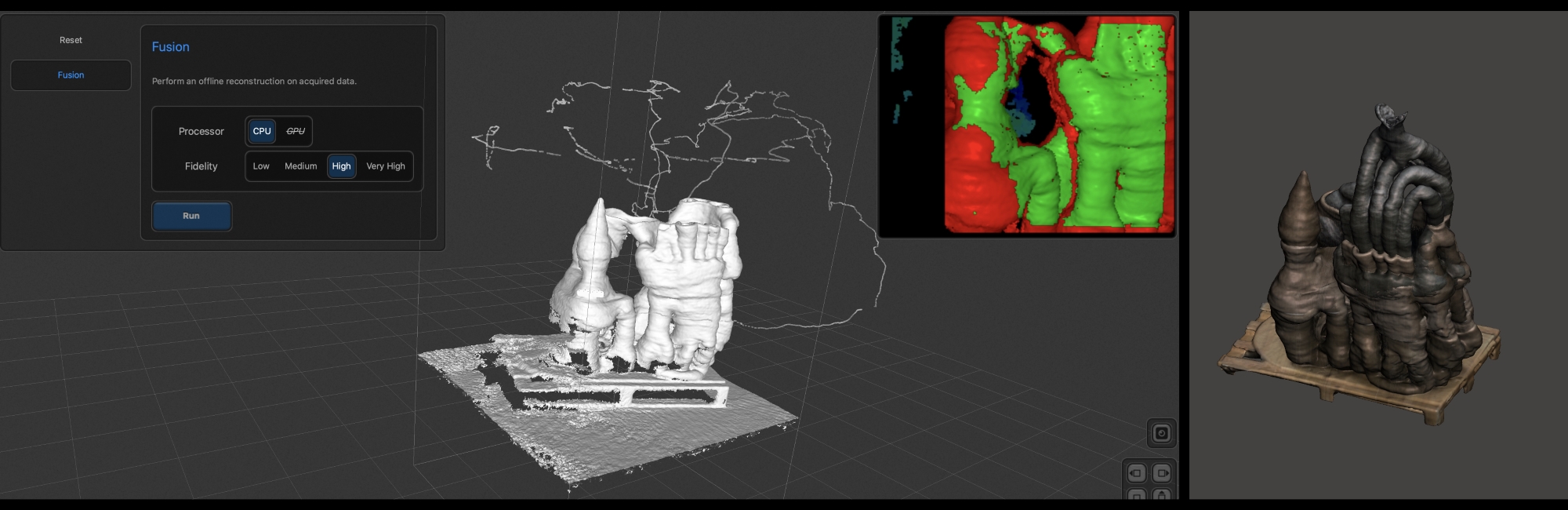
Pressing between the lines
Throughout the development of this three-year research project, I have maintained a connection to the process of hand-printing clay. This work embodies what Richard Sennett refers to as an ‘extended rhythm…that allows the craftsman to develop specific skills and rituals—duties performed again and again’ (Richard Sennett, The Craftsman, 2008). It is also something that can be measured by using various sensory technologies, such as 3d scanning and movement tracking.
My relationship with HPC was already well formed before I had seen the ceramic 3DP working (developed first by Studio Unfold and others, 2009). My body and closeness to the clay are removed and replaced by an automated machine.
I assumed I owned my experience but now I was observing it, watching it play out in front of me. This provided the motivation to understand the processes involved in printing an object. These stages in order are normally: CAD; SLICER; 3DP.
This led to me thinking about the sensory body changing through time and how that could affect the handmade object. As living beings, we (as well as animals and plants) make connections with our material environment through experience that manifests, often in hindsight, as meaning. On 28th May 2019, I interviewed Nicolas Pope whose practice takes a similar form to my own sculptural strand (figure 2) but is devoid of any technological mediation.
Early on in Pope’s interview, he remarks that he has Parkinson’s Disease and that it is very hard to control his actions; something he says is interesting in terms of the hand and material, as he is losing control of his own body. He values the mistakes in the work, something a machine cannot do.
“I am joyful when I go wrong. But if I purposefully try to go wrong, it becomes false. It’s why Parkinson’s is so great, I’m going wrong all the time.” (Pope, transcript, 2019, p4) I asked Pope how his forms come to be: do they come from the material or are they pre-designed?
“The forms created come from an entanglement of concepts, materials and forms that are put together when a group of pieces starts to make sense. The work comes from the material as much as it comes from the person making it.” (Pope, 2019)
This is a statement that makes sense when I think about my own form-making. Because of Pope’s ceramicist background, clay has always been his first-choice material and it has remained central to his way of working. Pope mentioned a simple but important point when we were trying to determine the value of the ceramic 3D printer, which is the regularity of the printed object and how its lines were not defined by touch but by the tool of the instrument:
“It’s very well made, without hesitation, without mistakes. I value mistakes. A lot of finger work is apparent. Finger work is really nice!” (Pope, 2019)
The most valuable and relevant insights from the interview are of Pope seeing himself as the instrument of making sculpture and drawings. He speaks of his own body being used by his instruction but also that he is not fully aware of the forms he wants to make and just going with the ‘flow’ (Csikszentmihalyi, The Psychology of Discovery and Invention, 2013). The body in his case is in decline, or ‘has the shakes’, which he sees as introducing the benefit of chance into his drawings. This is an irregularity that he likes – within the constructs he puts around himself. A robotic or mechanical process does not age the same way as an organic body. Its actions can be replayed in the same way 1,000 years from now if well-maintained and given the same code to follow. But Pope’s is a changing body that exists within a finite time frame. “I have no choice for Parkinson’s. My computers got fucked up. My antivirus is not working.” (Pope, 2019)
Our bodies perform an astonishing assortment of actions (Barbera Tversky, Mind in Motion, How Action Shapes Thought, 2019). The movements involved in this investigation alone include moving to stand, kneel, sit, walk, type, click the mouse, look up, look down, pull clay, coil clay, press clay, move clay, and operate various tools that in turn require their own movements to operate. These movements are broad outlines; they all require other movements within them, and they all operate in digital and physical space. These gestures without the physicality of clay are made digital in the world of computer-aided design. Algorithms have been created to twist and pull the digital form in simulated space. They have been built to express actions on design ideas and use only small, isolated movements of mouse clicks and keyboard shortcuts rather than the physicality needed to bring handmade things into the world. The next section offers a working solution to this sedentary way of interacting with computers so that my practice can better join these two opposing contexts.
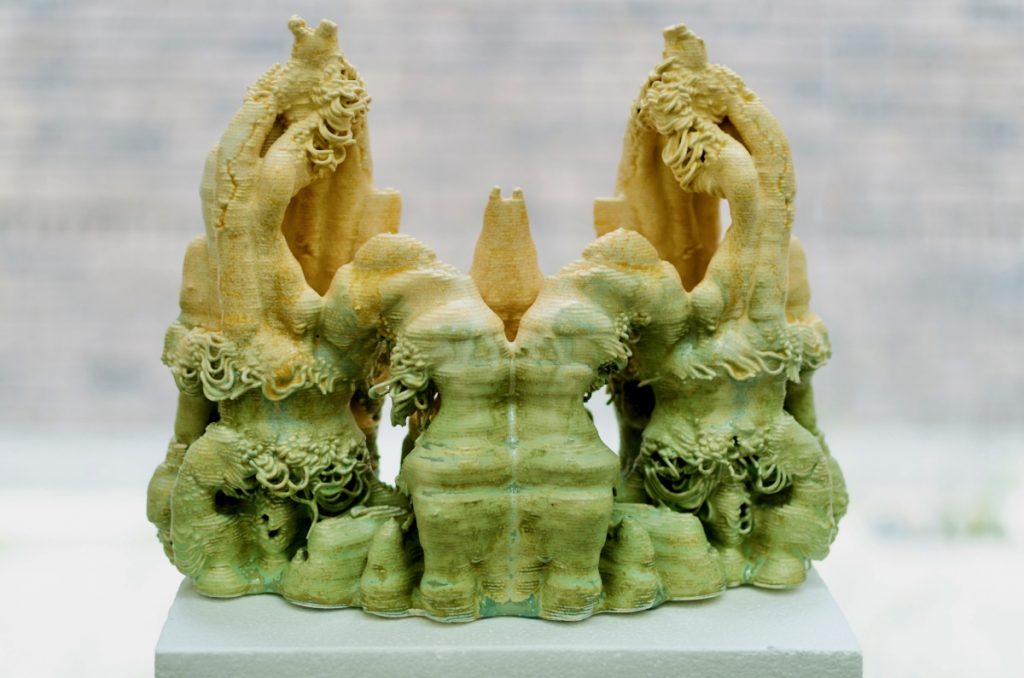
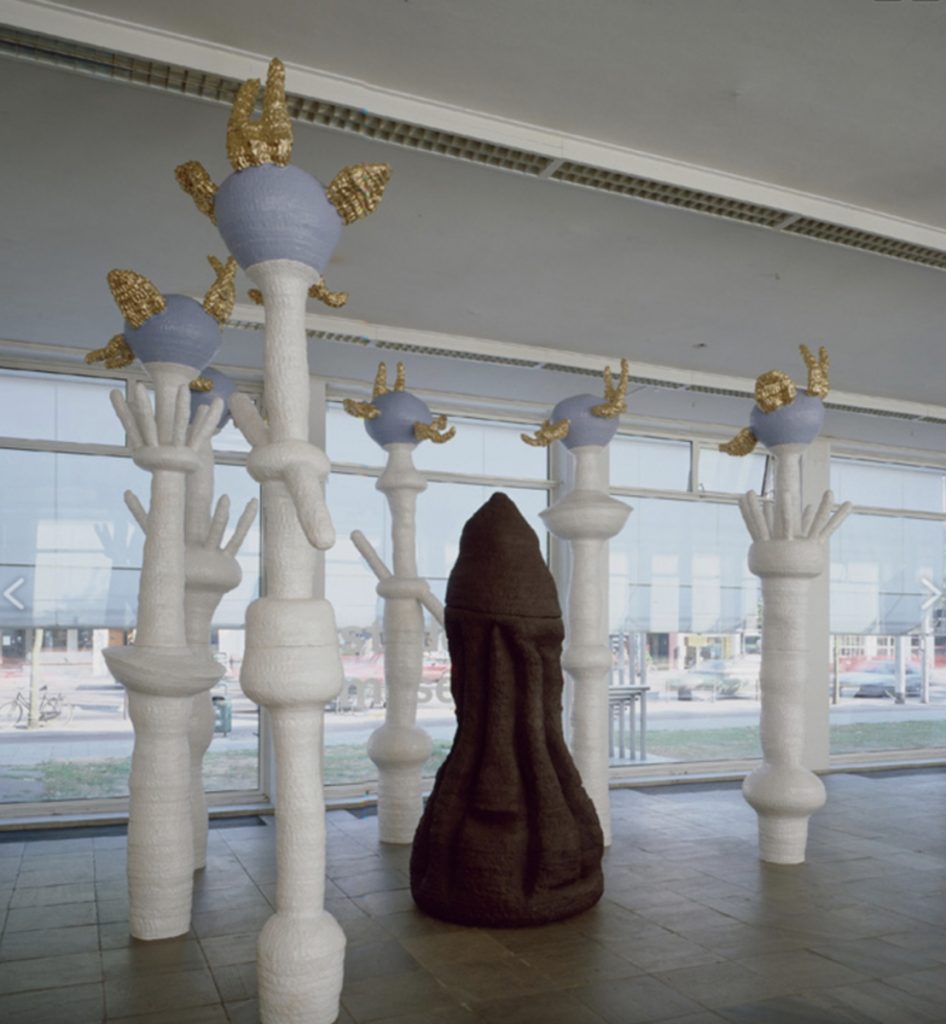

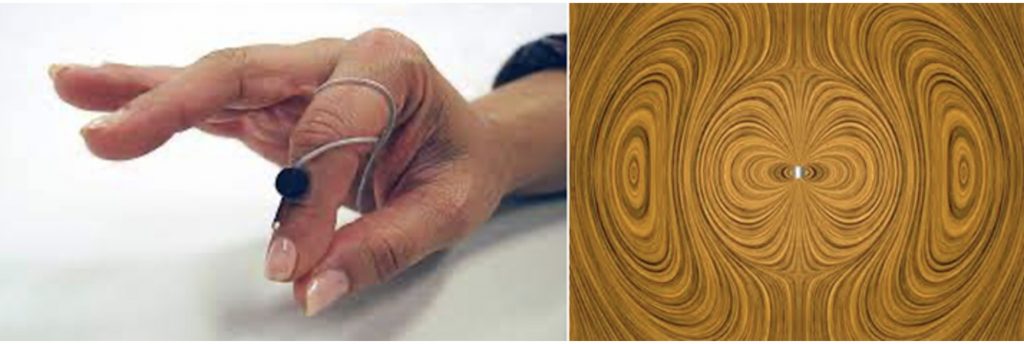
Hand-printing-clay and movement capture
This practical exploration intends to bring in a material connection to digital sculpture at the CAD stage. I intend to capture the experience of making using an electromagnetic tracking device, gathering layered movement data, and essentially turning myself into a 3D scanner.
By taking this approach I will be fusing the sculptural/material experience into the digital record. I hope that the digital object could then originate from a deeper, felt and more experienced place that can then utilize all of the spiraling possibilities afforded by digital fabrication. The 3D scanning methods I have used previously have required too many separate processes that can cause friction with one another across these physical and digital material boundaries.
They can slow down the flow of work. The emergence of robotics in the creative industries is revolutionizing how things are designed and made. They are transforming the culture of the spaces they inhabit (Willman, Block, Hutter, Byrne, Robotic Fabrication in Architecture, Art, and Design, 2018).
Another popular perspective, or feeling, is that automation and universality of mark-making within 3D printing is standardizing the objects it creates by following the rules set out by the machine’s author and different slicing programs. It allows everything to be measurable and quantifiable. The mistake can even be repeated! (Paul Virilio, The Original Accident, 2005).
If the aim is to get closer to the experience of the material and the bodily performance of making itself, then movement sensors could be the best way of recording the experience as well as the emergence of the sculpture.
In other CAD platforms that I am aware of, where a clay-type simulation is visualized, there is no possibility of linking it with the actual physical material itself. Creating a better interaction between the physical and digital spaces requires a lot of development. I required coders and specific hardware usually used in the domains of science and surgery. This blended practice, using the programming knowledge of Vicente Holler and Yingying Ying, who both wrote the Python script in response to my making and verbal directions, via a text editor plug-in for Grasshopper (a Rhinoceros 3D platform) that understands each point in motion captured by the tracker to draw the clay lines in digital space. Essentially, I was turned into a 3D scanner by utilizing hand-printing movements and the natural additive process of the emergent sculpture to build the digital model.
The unique position of HPC is that the practitioner is involved in the movement of creating the object whilst in contact with clay. The hands are involved in the emergence of the sculpture and so can be recorded by the tracking device (figures 3 and 4). This closer integration differs from the previously used 3d scanning devices because it utilizes the hand-printing movement as it interacts with clay. Observing the digital and material artifacts gives me confidence that the layered recording of these tacit movements captures the experience of making the sculpture in a fuller way than simply scanning the surface of the object. The simulated artifact has infinitely more surface detail than that of a scanned version and records internal surfaces, which reinforces the importance of this process as something that is unique, and different from 3D scanning.
When planning the project for EKWC, I found that the Grasshopper plugin (an algorithmic visual scripting program) had unfortunately been corrupted, and all the work that Vicente had done coding these developments was lost. It meant that I had to repeat the process with a different tracking system but also collaborate with a different person capable of coding in Python script as Vicente was not available. All this had to be done at a distance which created further parameters in terms of communication, responsiveness, and flow.
From my studio, I began spending time working on capturing the hand-printing data to collect enough information to build the grasshopper script. This sculptural form (figure 8) was first defined by the need to create internal shapes as well as external shapes and to understand the capability of the prototype to track through clay walls. Figures 5, 6 and 9 show the mesh-generating process. In figure 8 you can see an isolated section of the data showing the wavy motion which visualizes how I hand-print the clay onto the line beneath it. The algorithms created by the programmers measure the movement between a set of distance parameters that correspond to the pressure my thumb put on the clay. All other unwanted movements fall outside of the parameters and are automatically deleted. It means that nothing, but the HPC will be recorded.
This much more analytical process makes me acutely conscious of how I am interacting with the clay and the computer in tandem. There is a hyper-awareness of my making actions while engaged with two types of records. Defining my actions created small changes in the surfaces of the sculpture and affected the overall form as it did when 3D scanning some of my work leading up to this exploration.
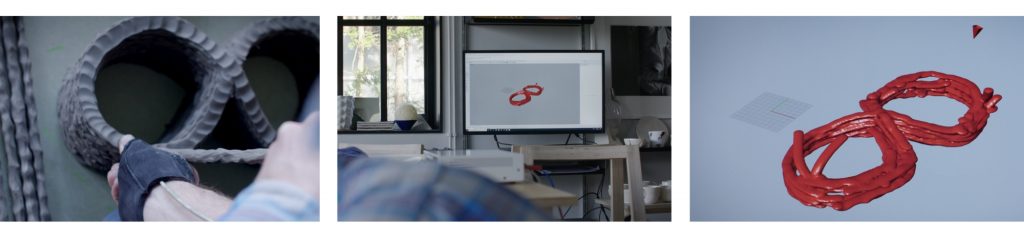
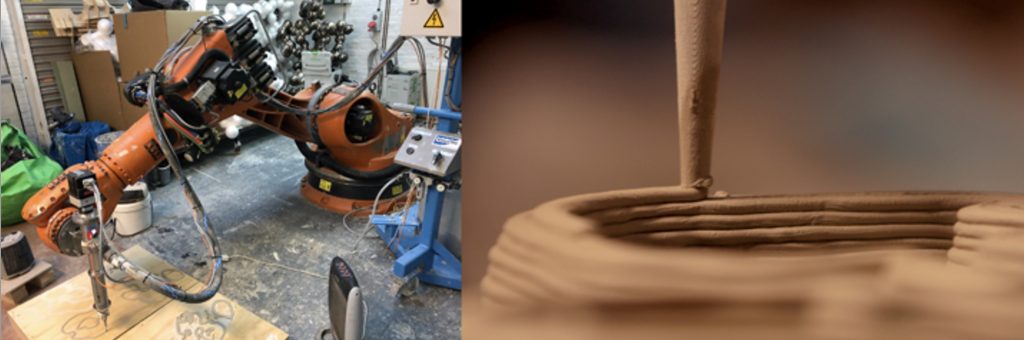
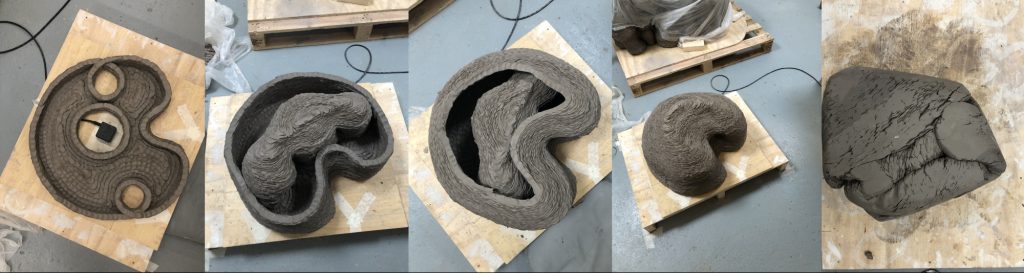
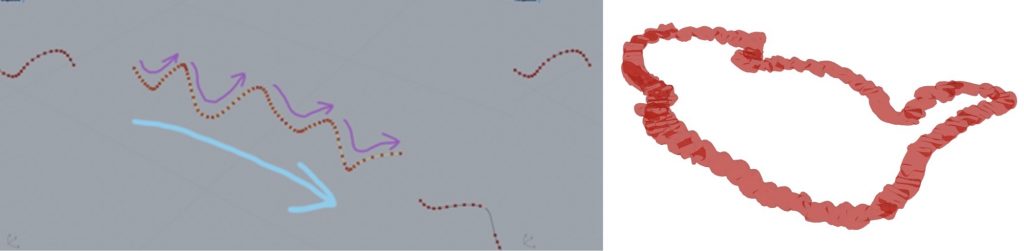
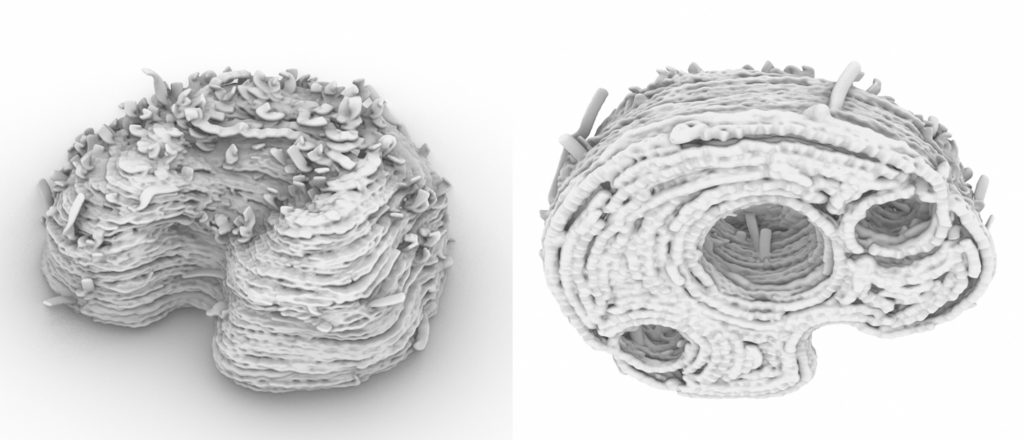
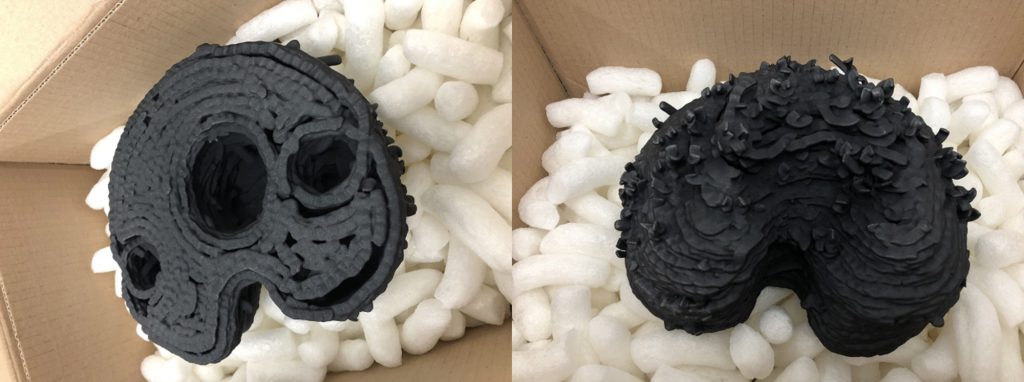
The additive nature of clay printing is especially good at translating into the digital space as it is in reversal. The coding algorithms consider the downward pressure of the thumb and the surface of the initial lines of clay so they can be pressed flat onto the surface of the ‘ground’ both in the physical and non-physical realms of materiality. The final mesh shows the entire layered experience of constructing the sculpture (figure 9). Internal and external spaces that could not have been achieved by scanning the sculpture are shown to be effective using this method of ‘movement scanning’. The movements that have changed the visual appearance of the digital clay are actions that are attached to the making experience and are ones that I see as beneficial in how the digital object can be expressed. The clay was reclaimed after it was used.
The clay has been through changes beyond this sculpture and will continue to go through changes as it is used again to record sculptural movement. The clay allows for instantaneous change and reaction that is reciprocal to the human senses. The digital object is then able to be printed at much smaller scales with very intricate details, compressing the physical movements recorded from the clay origin (figure 10).
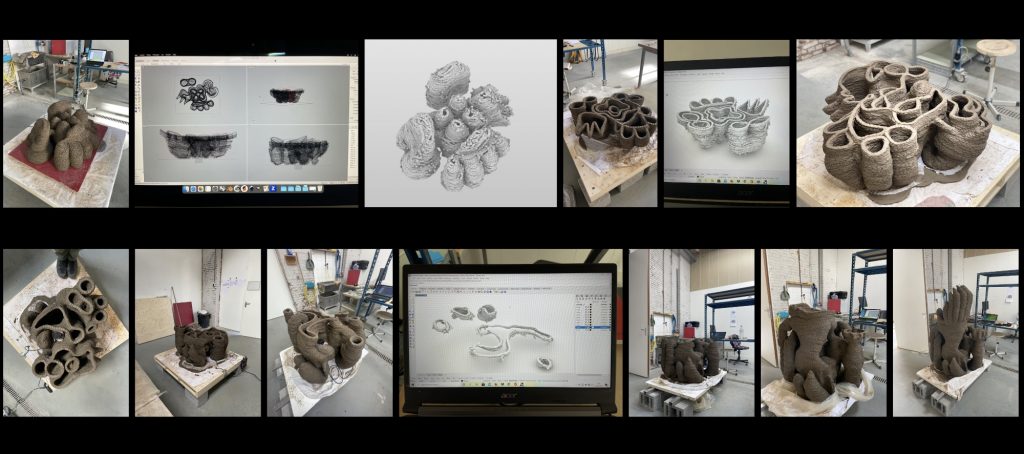
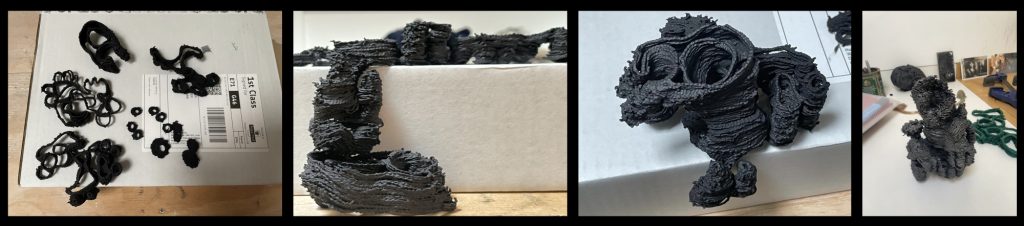
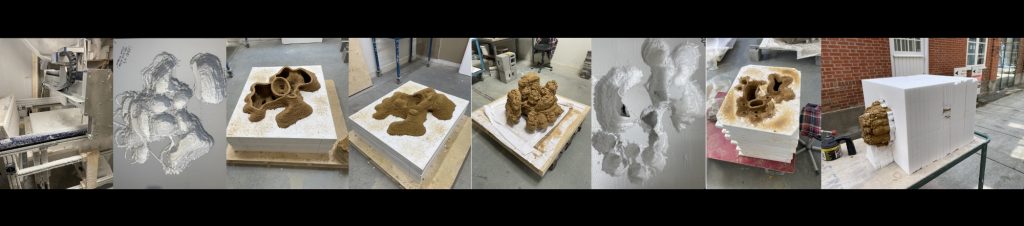
EKWC – Putting methods into practice
I could now put this into practice at EKWC to produce a large-scale hand-printed origin that is tracked from start to finish. The following images describe the process and the capabilities of this unique way of reciprocally producing both a physical and digital record of my movement.
Based on the measurements of the hand and the clay coil, the movements specific to this way of making have enabled a more meaningful digital record to take place, meaning that is, ‘incorporated and lived rather than simply intellectually understood’ (Juhani Pallasmaa, The Thinking Hand, 2012). In future projects, this could be expanded exponentially if given to other practitioners to work with whose practice can be measured through repeated movements. It would allow a unique response to cad design based on human interaction with clay.
For my sculpture, this blended way of thinking about material has enabled the internal structure to be recorded as it is experienced, which has resulted in an unusual formal digital development that is different from standard scanning devices. It will no doubt have interesting future fabrication consequences, utilizing CNC, 3D printing, and robotics.
The unexpected capture of other repeated movements that are not visible in the physical origin could also be a source of future inspiration that can guide this developing language in both the digital and physical realms.
The focus on detailing the movements of hand-printing clay has led to a hyper-awareness of the actions that I am involved in. Some of the parameters have altered the way that I make the sculpture, sometimes having to change the direction of movement so that I don’t have to change hands so that everything can be recorded. This explicit example of how technology can define a direction of thought through mediated instruction is another important reason for needing to understand these systems from the inside out.

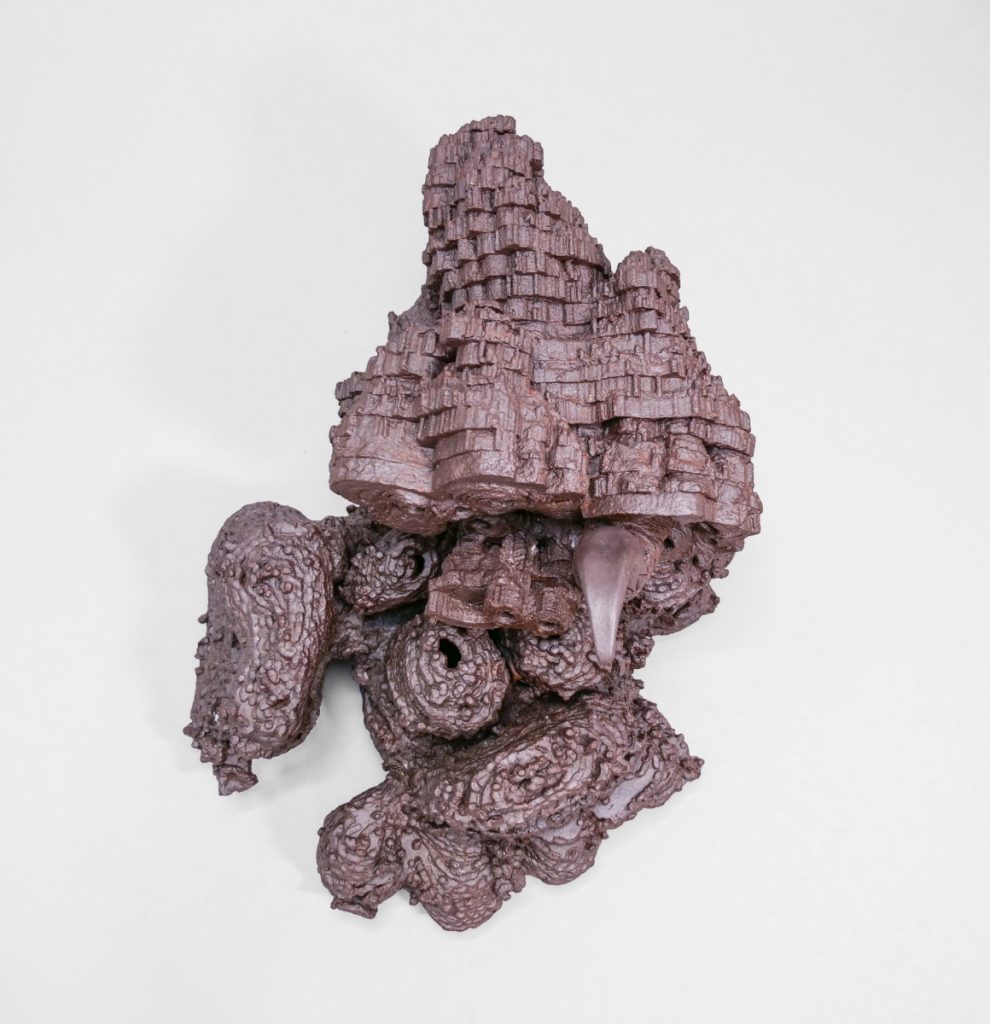
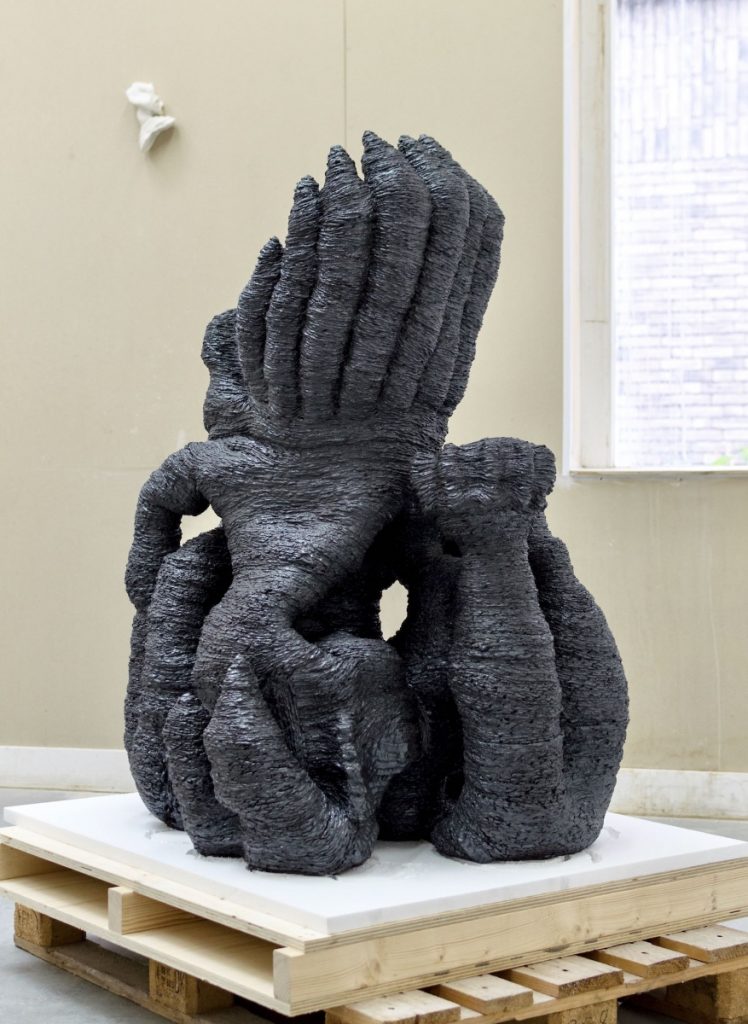
Summary
This approach intends to change the direction of travel for CAD: not following the direction of a desk-based beginning, but with a connection to the material and labor that is essential in bringing something physical into the world. It enables a connection we need to get back, that helps promote care and understanding for what is produced. The fields of fine art, fabrication, design, architecture, craft and human-computer interaction can benefit from this research, with crossovers occurring in many other academic disciplines. This project gives practical examples of integrating varying levels of hand-making into the space of Rhino CAD (multidisciplinary platform) and the 3D printing process. This way of linking movement to an aging and forever-changing body can also affect the language that machines produce, to be less perfect and more attuned with our living origin.
Acknowledgments
3D printing backwards has only been possible with funding from the Arts and Humanities Research Council, UK. It has been enabled by computer programmers Vincente Soler (UK) and Yingying Ying (University of Michigan US). Making workshops Grymsdyke farm (UK) and EKWC (Netherlands). The conduit hardware that I used to make the digital sculptures was supplied by Target 3D and Polhemus Electromagnetic Tracking (EMT), Rhino 3D (CAD program), and Clay 3D Printers LUTUM and WASP. This research was conducted whilst on the CDT research program, a Ph.D. partnership between Northumbria University and the University of Sunderland.
Biography
Theo Harper is an artist and researcher based in Northumberland. His practice spans site-specific installation, sculpture, video, and photography. Clay is always at the center; Theo interrogates material and processes, intuitively inventing ways to release an expressive making narrative. It is a constant inquiry: Born out of repetitive, time-consuming, and layered techniques. By mastering different making systems, it is possible to break apart pre-existing realities.
Theo studied sculpture at the Royal College of Art, London. He has shown work nationally and internationally and taken part in various residencies. Alongside gallery-based exhibitions, he has organized various projects that include a permanent installation in a Victorian terraced house, in London (2013-16) and a cliff polishing in Cornwall (2014). In 2021 he completed a three-month project at the European Ceramics Works Centre, Netherlands (2021). In April 2022 Theo completed a practice based PhD titled ‘A Hybrid Origin; re-thinking computer aided design through hand-printing clay’.
Visit Theo Harper’s website and Instagram page.
References
Books
[1] Bennett Jane. Vibrant Matter, a political ecology of things, Duke university press, United States of America 2010 // Vallgårda, A. (2009) Computational composites, understanding the materiality of computational technology. PhD Thesis. Copenhagen: Royal Danish Academy of Art // Ingold, Tim (2013). Making, Anthropology, Archaeology, Art and Architecture. Routledge.
[2] Sennett, R (2008) The Craftsman, New York: Penguin
[3] Pope transcript, interviewed and recorded on the 28th May 2019
[4] Csikszentmihalyi, M. The phycology of discovery and Invention, Harper Perennial, (2013)
[5] Tversky, B (2019) Mind in Motion, How Action Shapes Thought, Basic Books, New York
[6] Willmann, J. Block, P. Hutter, M. K Byrne, K. (2018) Robotic Fabrication in Architecture, Art and Design, 2018
[7] Virilio, Paul (2005). The Original Accident, Polity Press
[8] Pallasmaa, Juhani (2009). The Thinking Hand. John Wiley and Sons Ltd
Photo captions
- Fig 1; Photogrammetry scan, self-holding clay, 2021
- Fig 2; A generic sedentary design practice not in contact with physical material (https://www.arenasolutions.com/resources/glossary/computer-aided-design/ )
- Fig 3; Hand-printing-clay in action, link to time-lapse https://vimeo.com/512429824 , studio, 2021
- Fig 4; 3D scanning in motion, studio, 2021
- Fig 5; Guard, 3D printed ceramics, 21x12x27, EKWC, 2021
- Fig 6; Yahweh and the Seraphim (1995), Glazed and lustred ceramic Height: 430 cm | 169 in Installation view, Stedelijk Museum, Amsterdam, 1995
- Fig 7; Hands, Touch, Clay
- Fig 8; Magnetic movement tracking sensors, https://polhemus.com/applications/electromagnetics/
- Fig 9; Prototype 01, Movement tracking set up, link to demo https://vimeo.com/413878714 Grymsdyke farm, 2020
- Fig 10; Printing clay using robotics, link to demo https://vimeo.com/413878905 , Grymsdyke farm, 2020
- Fig 11; Prototype 02, movement tracking hand-printed-clay, studio, 2021
- Fig 12; Isolated movement of one hand-printed clay line, studio, 2021
- Fig 13; 3D digital record of clay movement, studio, 2021
- Fig 14; Digitally printed emergent clay form at 1/20th of the scale, nylon, studio, 2021
- Fig 15; Process into practice, building a full-scale hand-printed sculpture, EKWC, 2021
- Fig 16; Derived from the clay origin, Digital 3D render, EKWC, 2021
- Fig 17; Nylon prints, taken from the movement data, studio, 2021
- Fig 18; CNC milling the captured lines of movement and then hand-printing back into the polystyrene mold (with thanks to Sander Albas and EKWC, 2021)
- Fig 19; Jest, Derived from the Origin, Ceramic, 74 x 65x 79, EKWC, 2021
- Fig 20; Origin, Ceramic, 128x 88 x78, EKWC, 2021