By Hendrien Horn
As clay 3D printing has started to become popular amongst some potters, it has become a topic of debate, which can, at times cause some opposing opinions. Furthermore, I think that once an artistic process is better understood, the doors for a healthy conversation can open. As a potter who has worked with both “traditional” and “technological” techniques when it comes to my clay works, I feel I can vouch for both sides of the aisle.
My background in clay started with sculpting and wheelwork, which I practiced for many years. It was only when I injured myself while working on my pottery wheel that I looked for other avenues to explore. It was 2019, and clay 3D printing was just starting to take hold across the world. I propelled myself into this new artform as I slowly started to change my preconceived ideas of technology and how it can be used to create art.
My assumption that 3D printing in clay would be easier as a potter was quickly disproved. The physicality of prepping the clay, setting up the machine, plus all the other processes required before even starting to print – was something I did not account for. After taking the time to teach myself how to 3D design on a computer, I finally purchased my clay 3D printer in 2021. This was followed by many months of testing my clay consistency, experimenting with form, and learning how the 3D printer operates – all before I could even start to find my way as a contemporary artist.
Often misunderstood, the clay 3D printer is considered a tool, much like the pottery wheel and electric kiln. As with any tool, the learning curve for any potter can be steep, and as my personal experience has shown, the same can be said for 3D printing in clay. Along with an understanding of the full pottery process such as; handling of the clay material, decorating and kiln firings – an understanding of how to create a 3D model and preparing it for 3D printing is also required.
It may come as a surprise to learn that some of the first 3D printers built and modified to 3D print with clay were designed and fabricated by artists and not only by engineers.
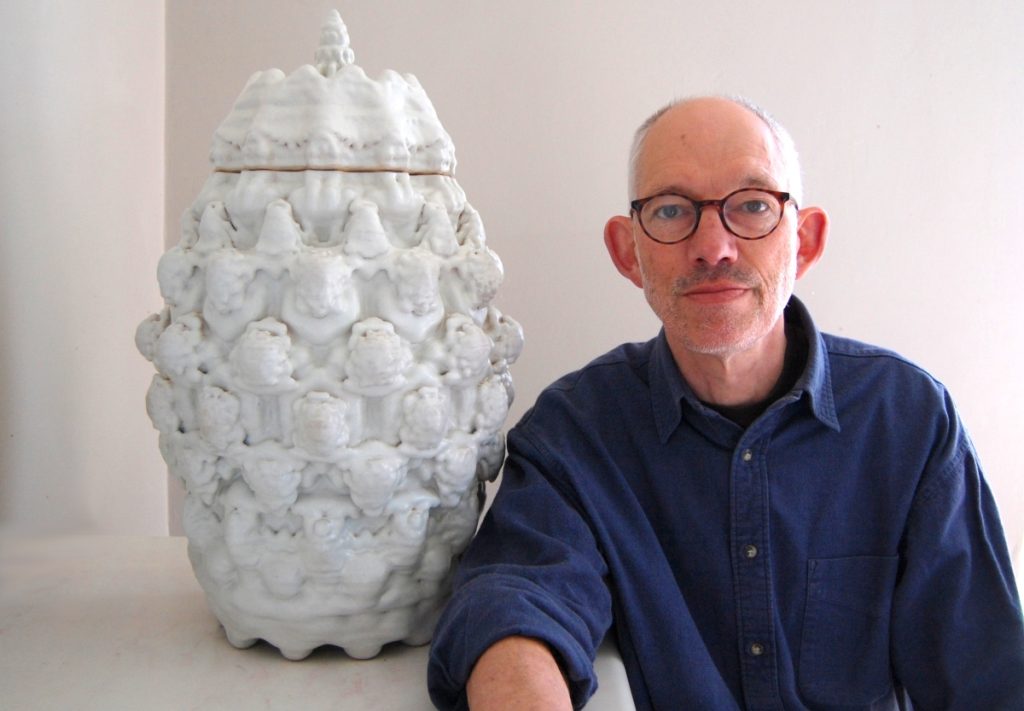
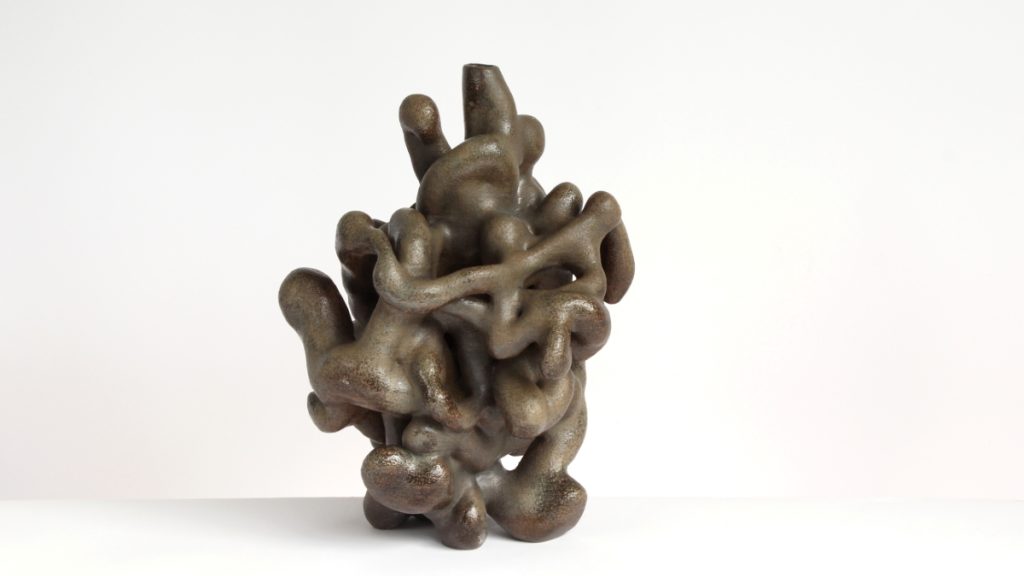
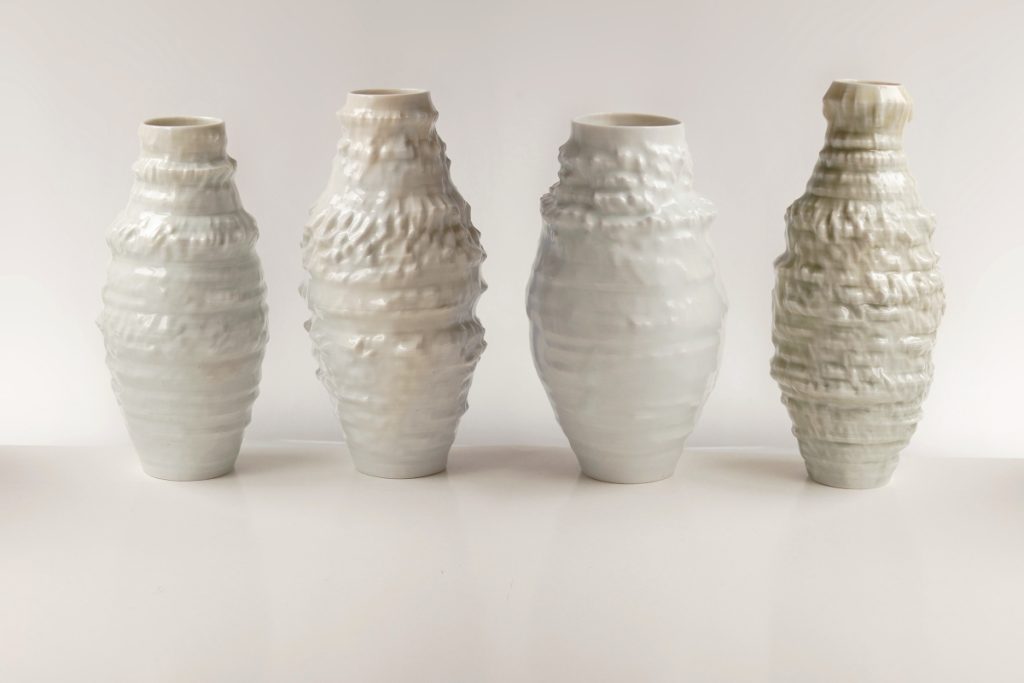
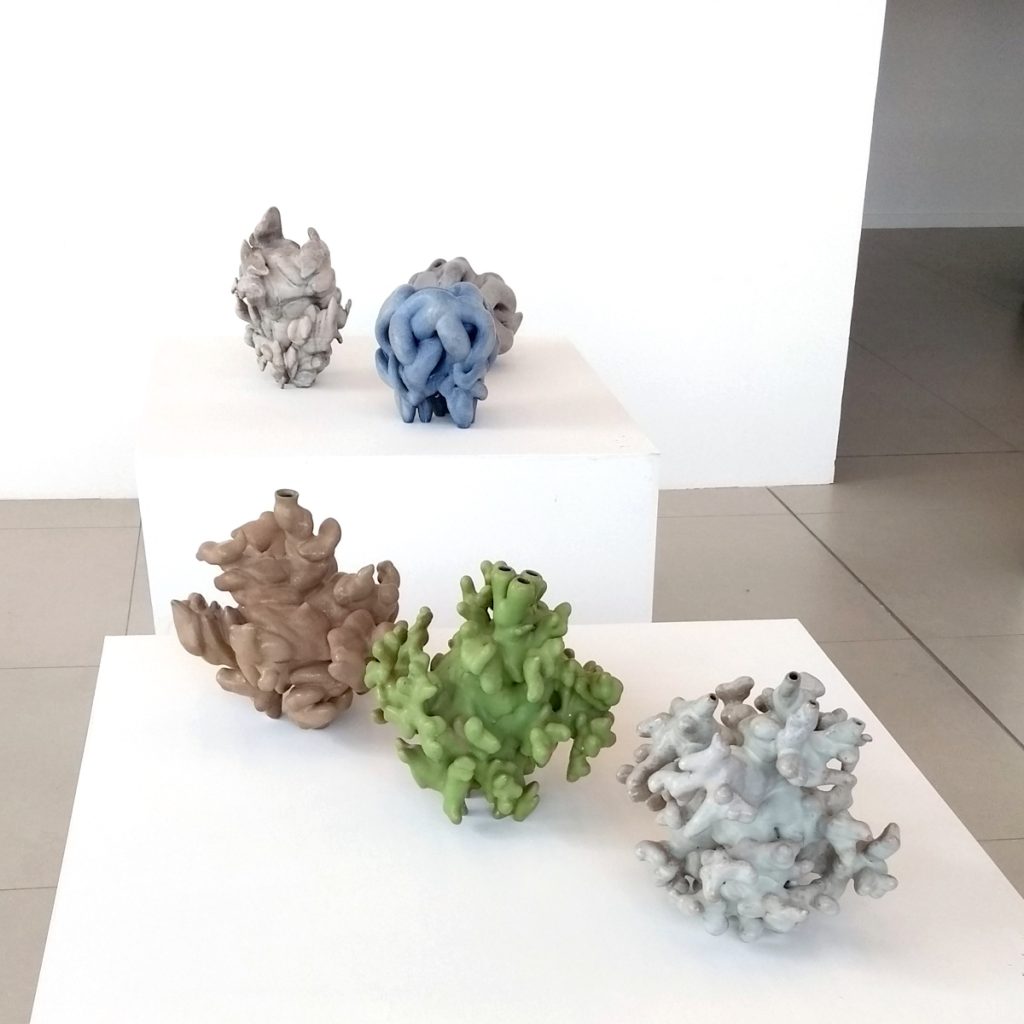
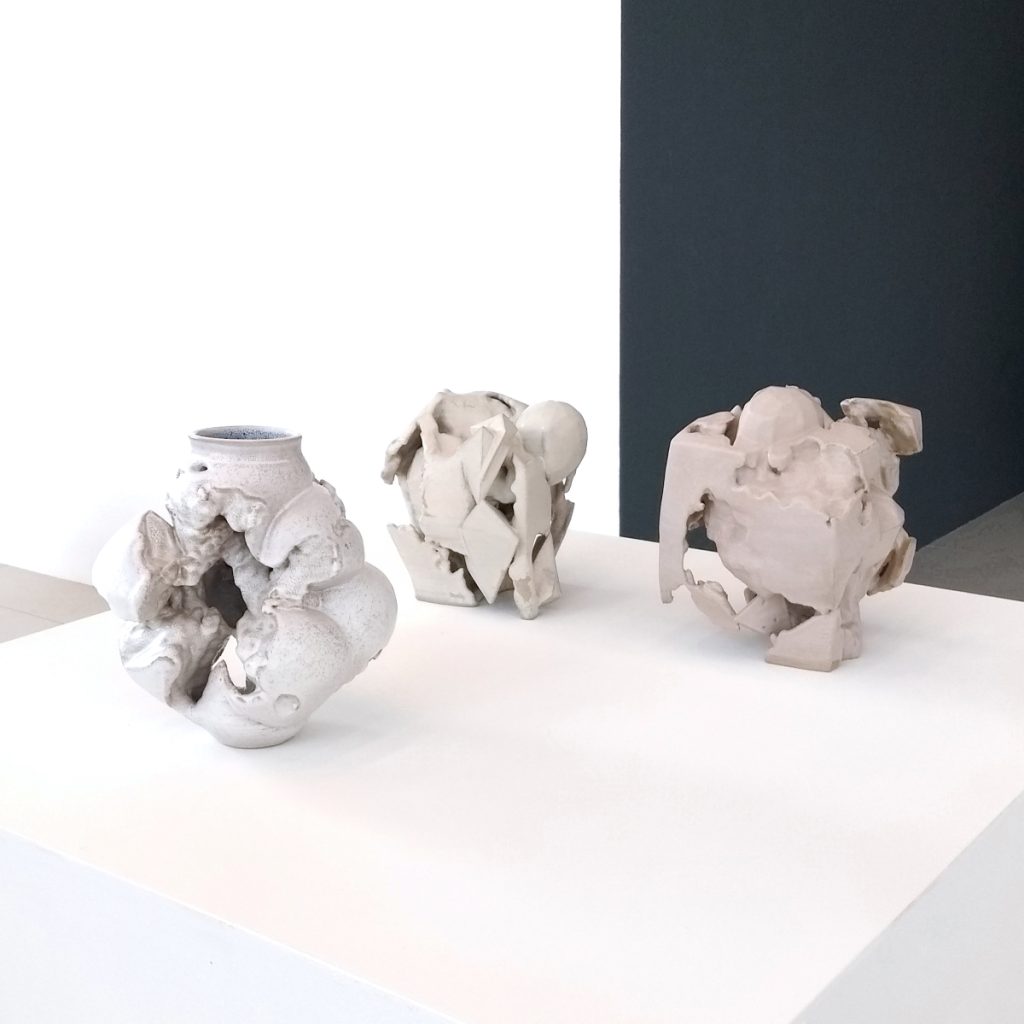
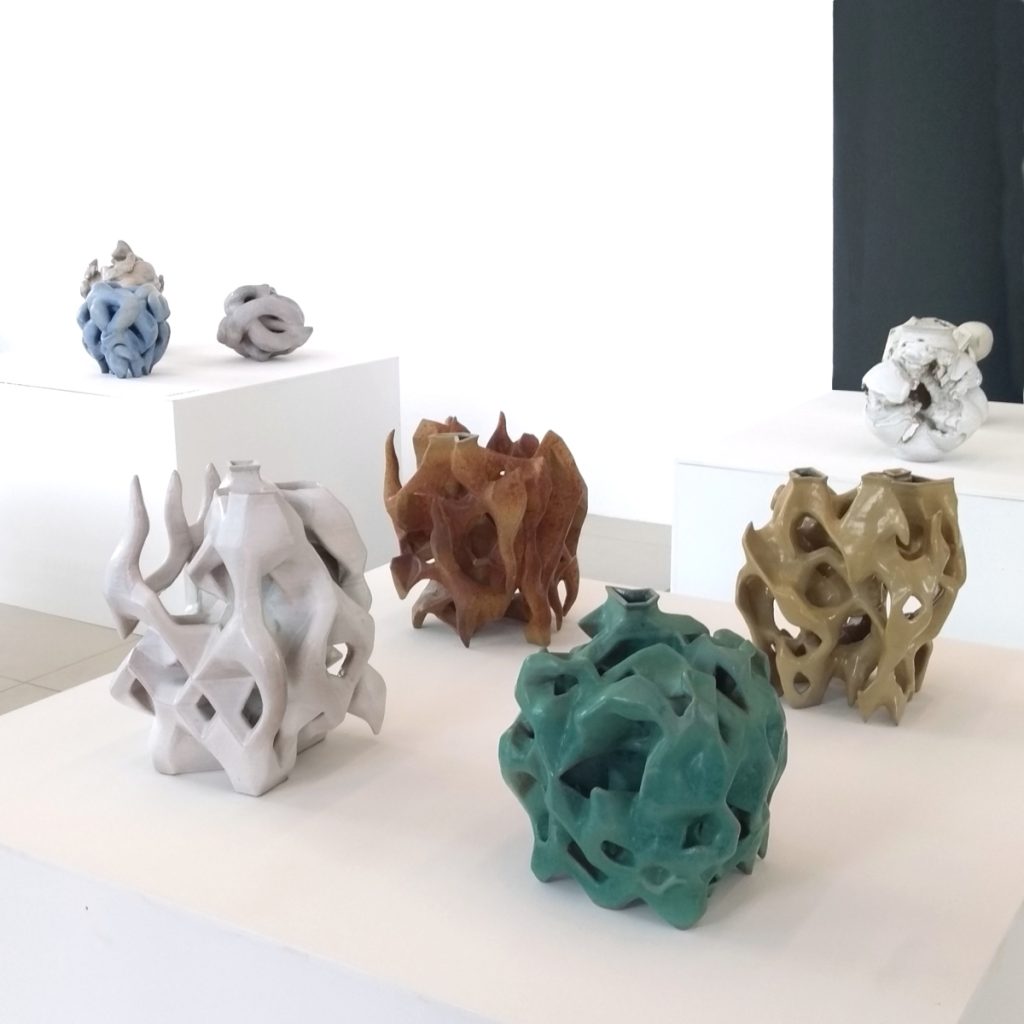
As one of the pioneers in the clay 3D printing industry, Jonathan Keep is a renowned artist who has paved the way for many. After receiving his MA from the Royal College of Art in London, he went on to design and build his own ceramic 3D printer, making the build instructions freely available online. With the use of advanced technologies, he strives to create clay forms that “question the reality we create for ourselves”. Jonathan is “quietly” working to normalise the idea that clay 3D printing is just the next step in the evolution of pottery, much like the introduction of the electric pottery wheel in the early 1900s.
Advancements in technology and the practice of art have always been intertwined. No matter what your ideas of art are, they will forever change as artists explore new ways of expressing themselves.
Taekyeom Lee is an award-winning designer who is also an assistant professor of Graphic Design at the University of Wisconsin-Madison. He built his own ceramic 3D printer and views clay as a type of ink, creating “tangible typography” with his 3D-printed works. Making a memorable remark in one of our discussions when he said; “Don’t you think that if Da Vinci had access to these new technological tools that he would not use them?”. It is a fair comment to make, and I am sure some may disagree… but it does, however, make one think.
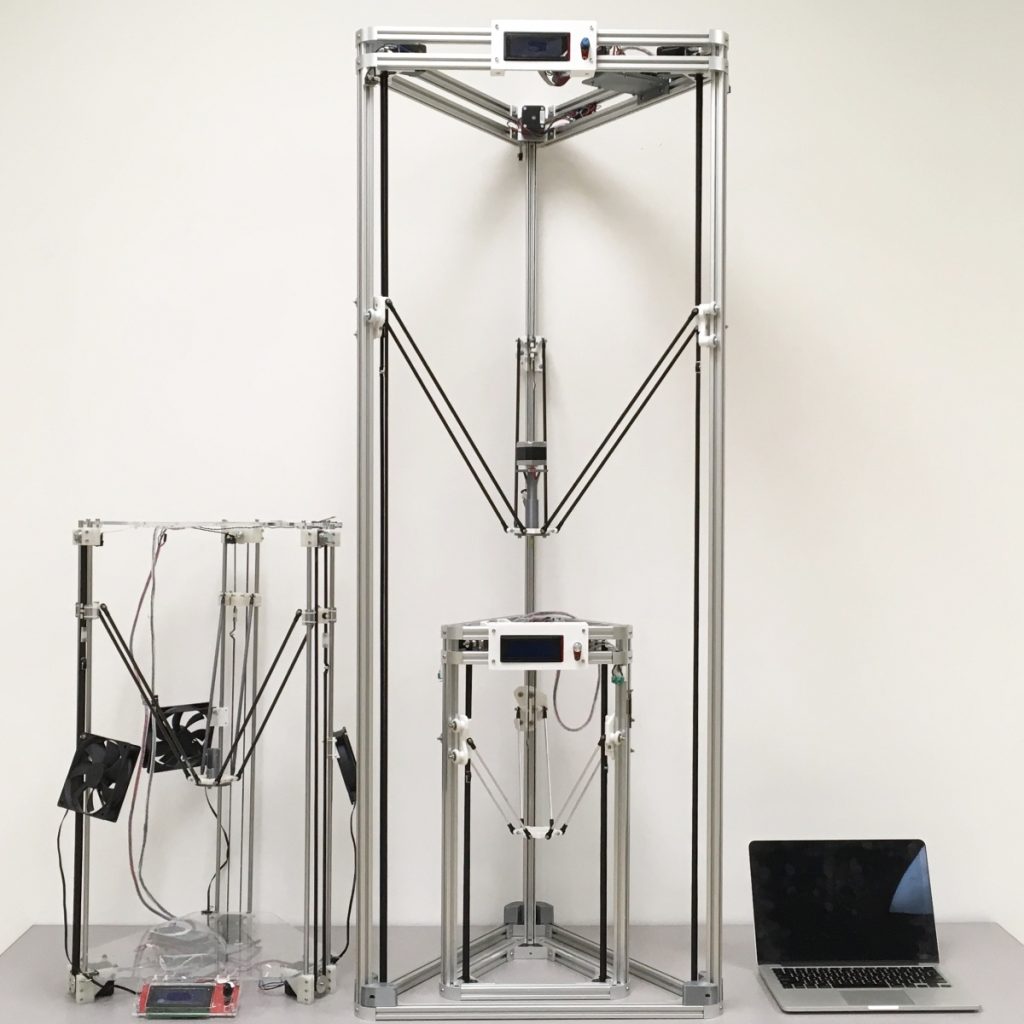
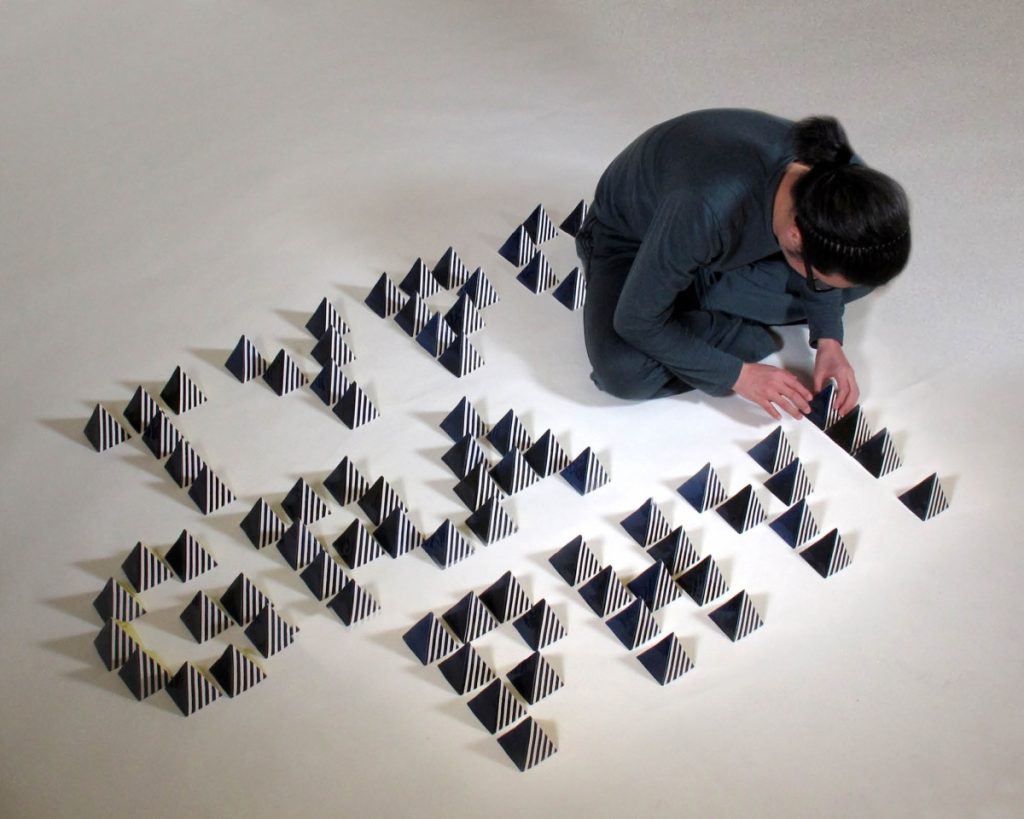
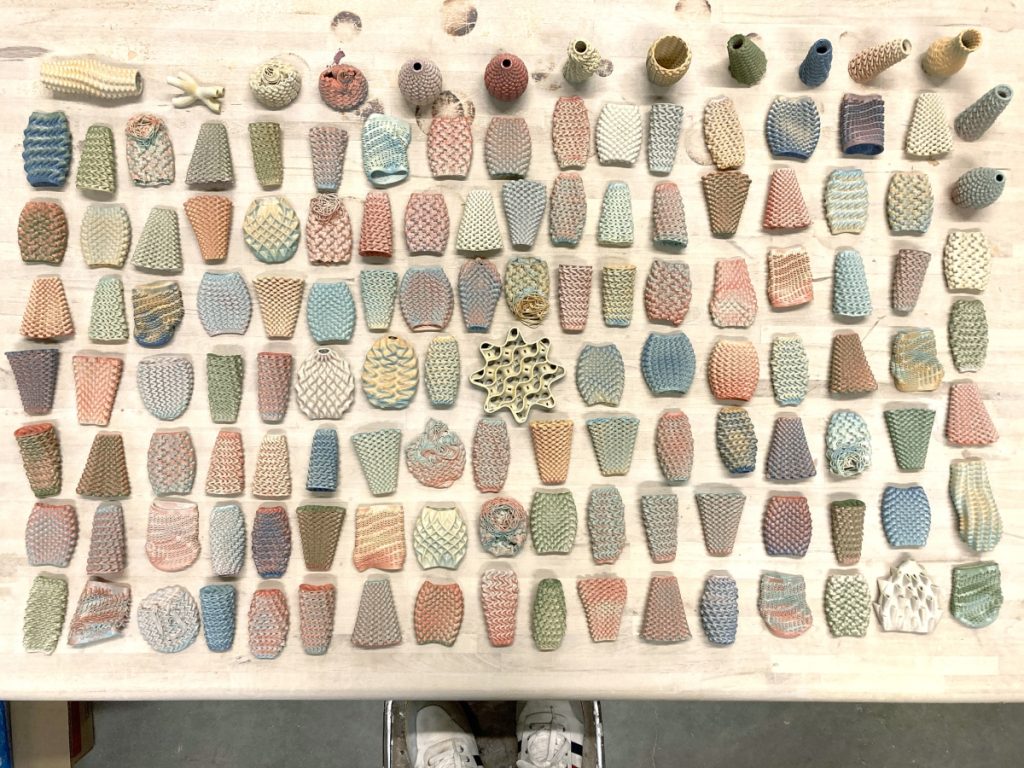
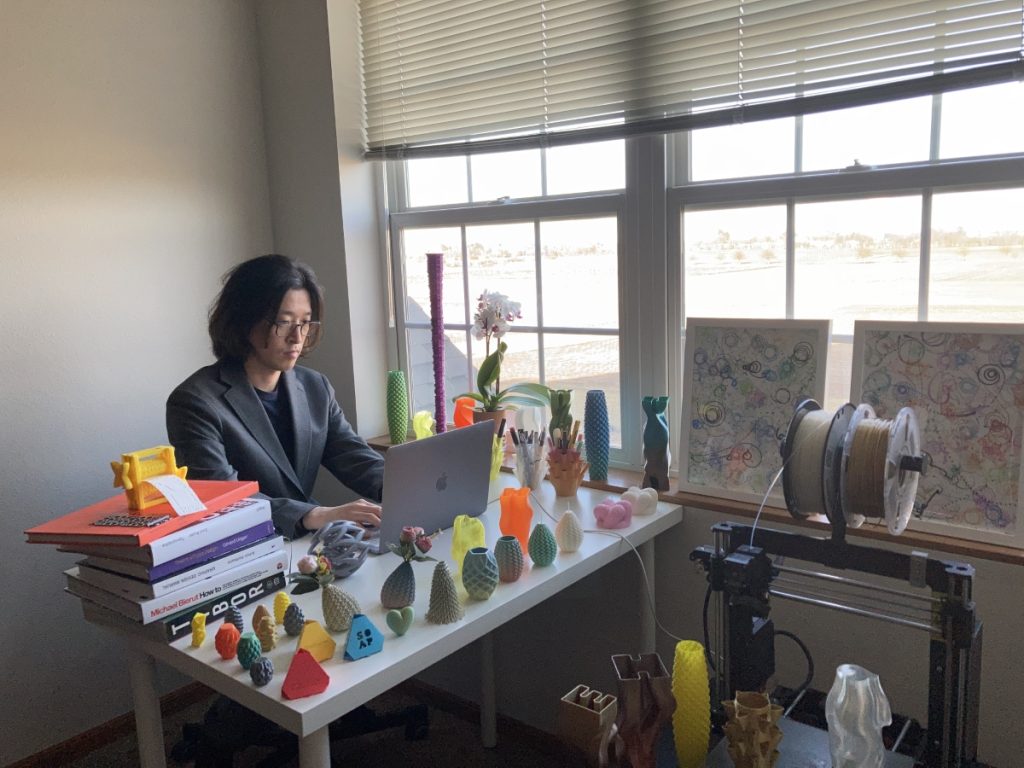
If you break it down, the two techniques of creating clay forms with the use of a pottery wheel and a 3D printer share some similarities, even if the execution thereof is different.
A potter creating a form on the pottery wheel starts with a compressed ball of clay that is pulled and sculpted by hand whilst the pottery wheel is in motion. The stability that the pottery wheel affords – along with the required speed controlled by the potter, directly relates to the forms that the potter can achieve. This takes skill and practice. Once the form is finished, it must be left to stand and dry until it is ready to be sculpted and decorated using the desired techniques followed by the final kiln firing processes.
A potter using a clay 3D printer must sculpt a form in a CAD (computer-aided design) software and prepare the 3D model for printing. Setting the 3D printer speed and how much material must be extruded are only some of the important preferences to consider. These directly relate to the accuracy of your 3D printed forms, and take practice and skill to master. The clay then needs to be compressed into a container, making it ready for printing. With a few adjustments to the printer, you can start your 3D print. The printer uses the coiling method, with the print head moving and extruding the clay material, layer by layer. Once the 3D print is finished, it needs to be left to dry until it can be sculpted and/or smoothed, decorated, and kiln-fired.
Looking at the above techniques, making something using a 3D printer instead of a pottery wheel can, in many cases, take longer. The idea that all 3D printing is related to mass production is sadly the biggest misconception. Large industrial-sized machinery and manpower are required to mass produce products, and this is not achievable by a single potter using a 3D printer in their studio.
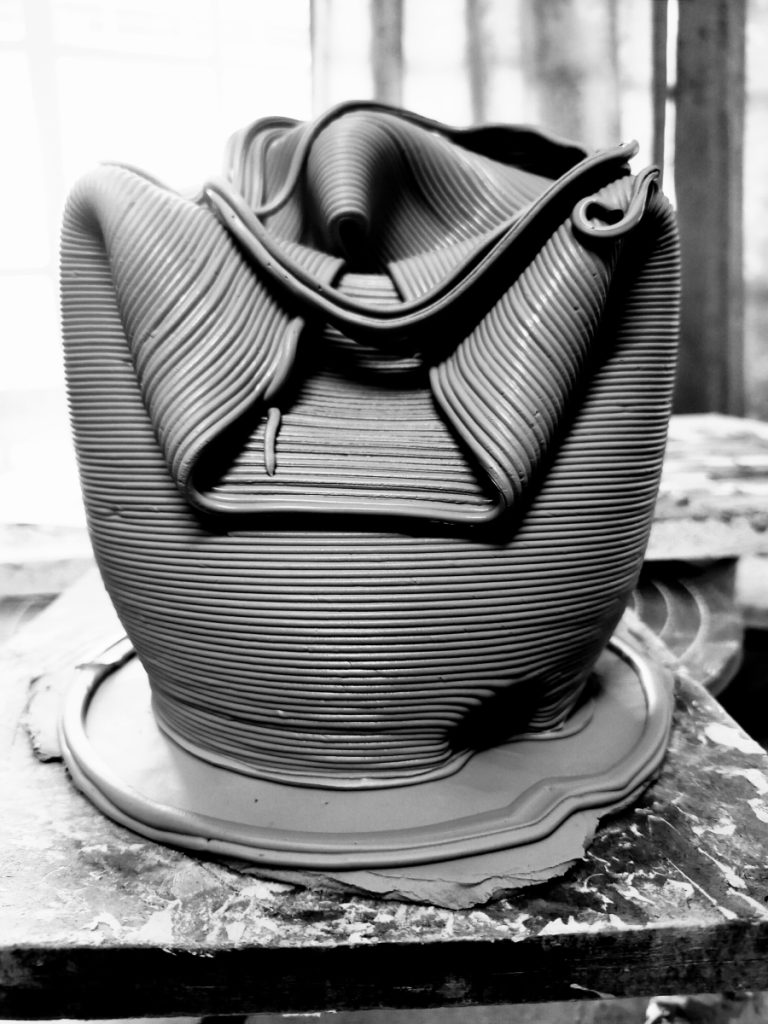
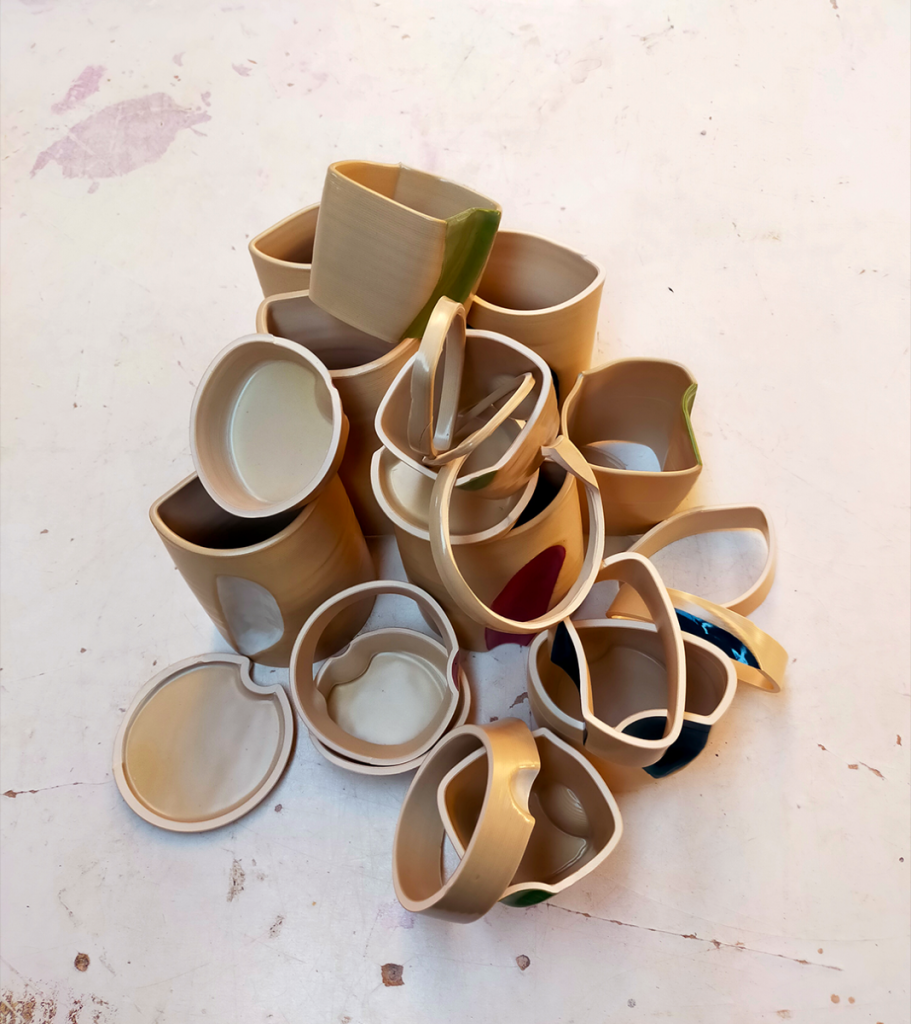
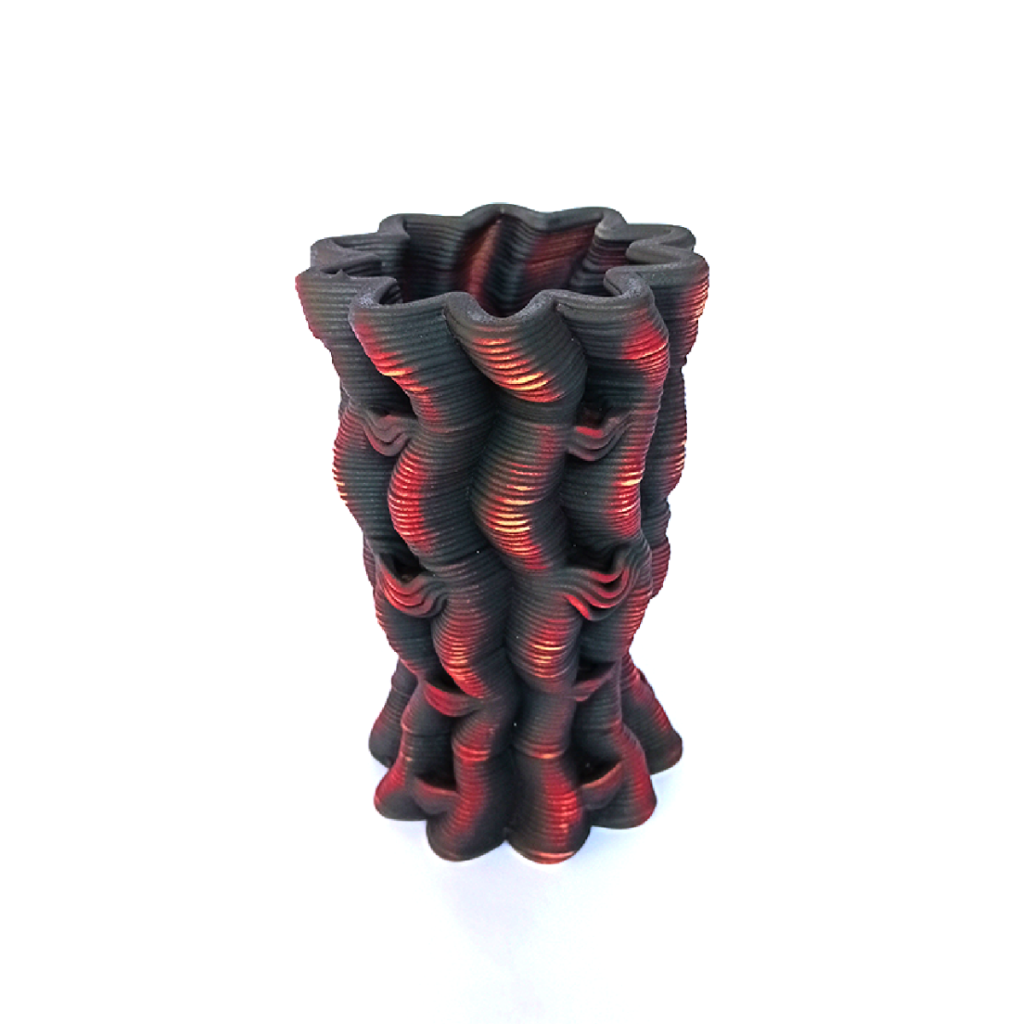
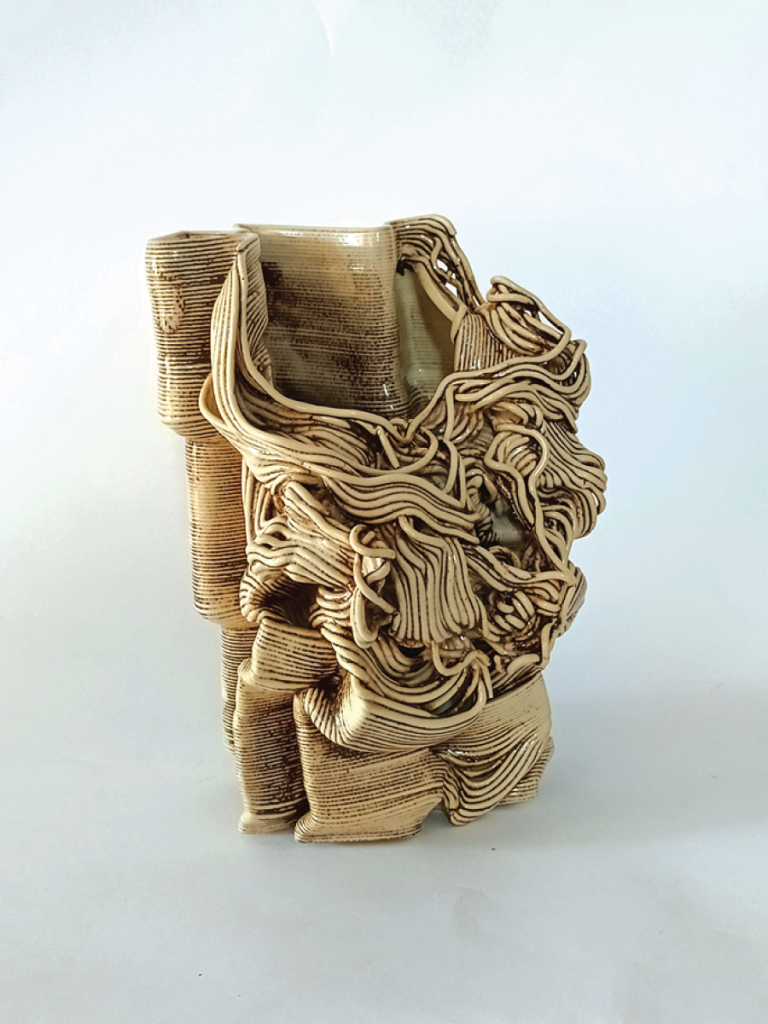
A great example is slip casting. Potters pour wet clay into a pre-made plaster or silicon mould creating a uniformed clay form, which can be made as a stand-alone piece or produced repeatedly. How dissimilar is this technique from 3D printing a form repeatedly or using the 3D-printed form to create a plaster mould?
3D printing is widely known as a rapid prototyping technique. This refers to the ability of the maker to 3D print items at a faster rate than if you were to pay a company to manufacture the same product for you. Many hobbyists choose to buy FDM (fused deposition modelling) 3D printers, with some being relatively inexpensive and easily able to fit on a table. The difference between 3D printing with filaments that must be heated and melted during the printing process, and clay, vastly differs. The printers perform the same task but are engineered differently. A clay 3D printer can use either air pressure or a mechanical system to push the clay through the extruder mechanism and does not require any heating.
Contrary to popular belief, high precision clay prints that are identical to filament 3D prints are very difficult to achieve.
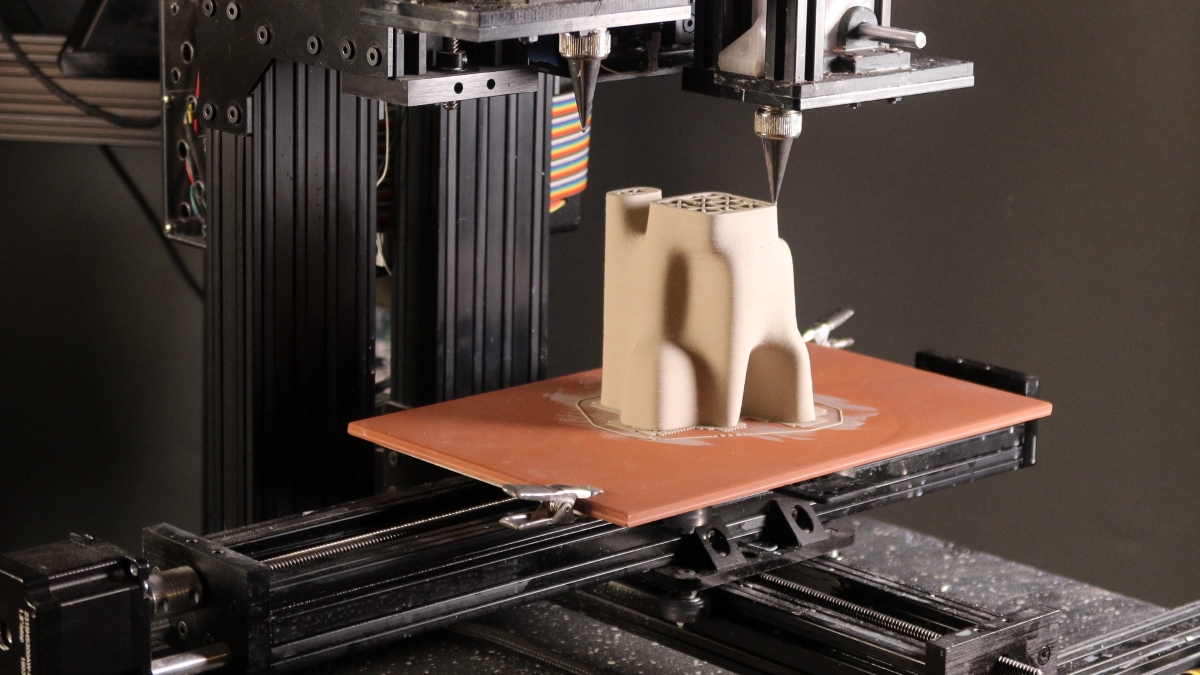
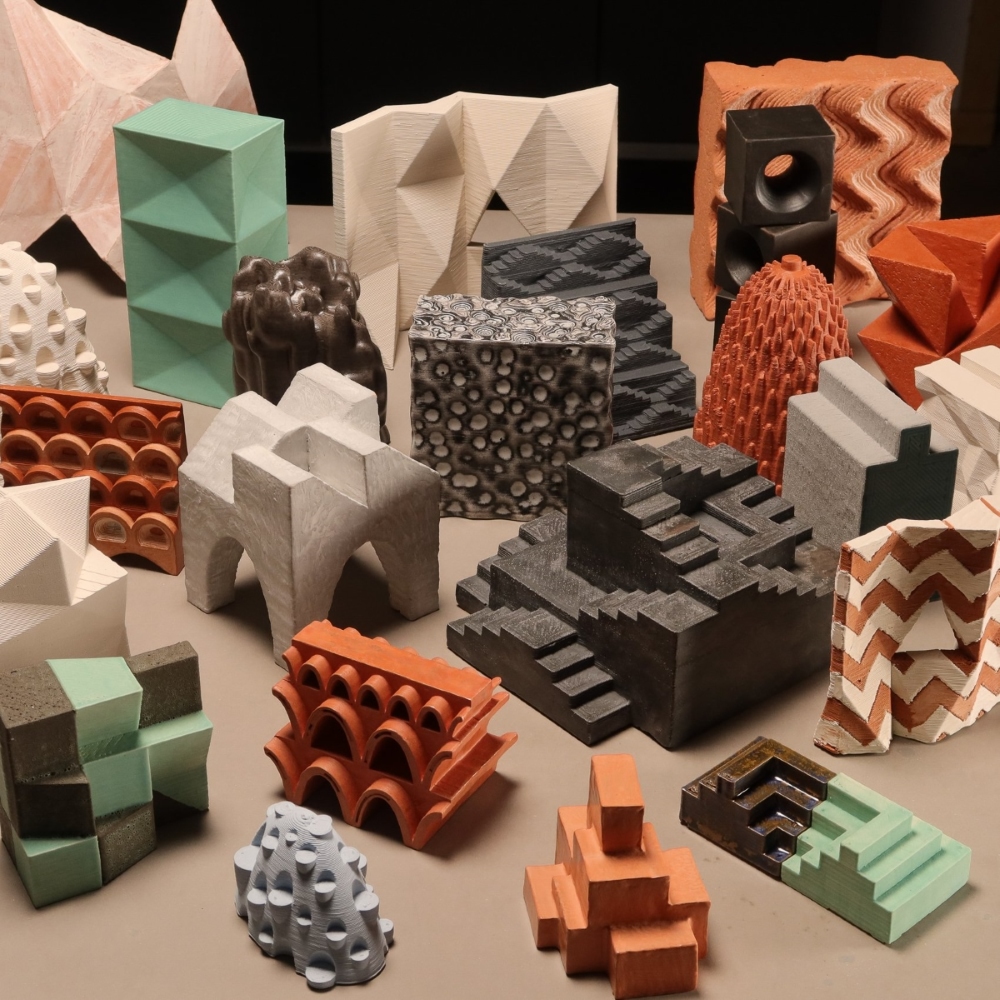
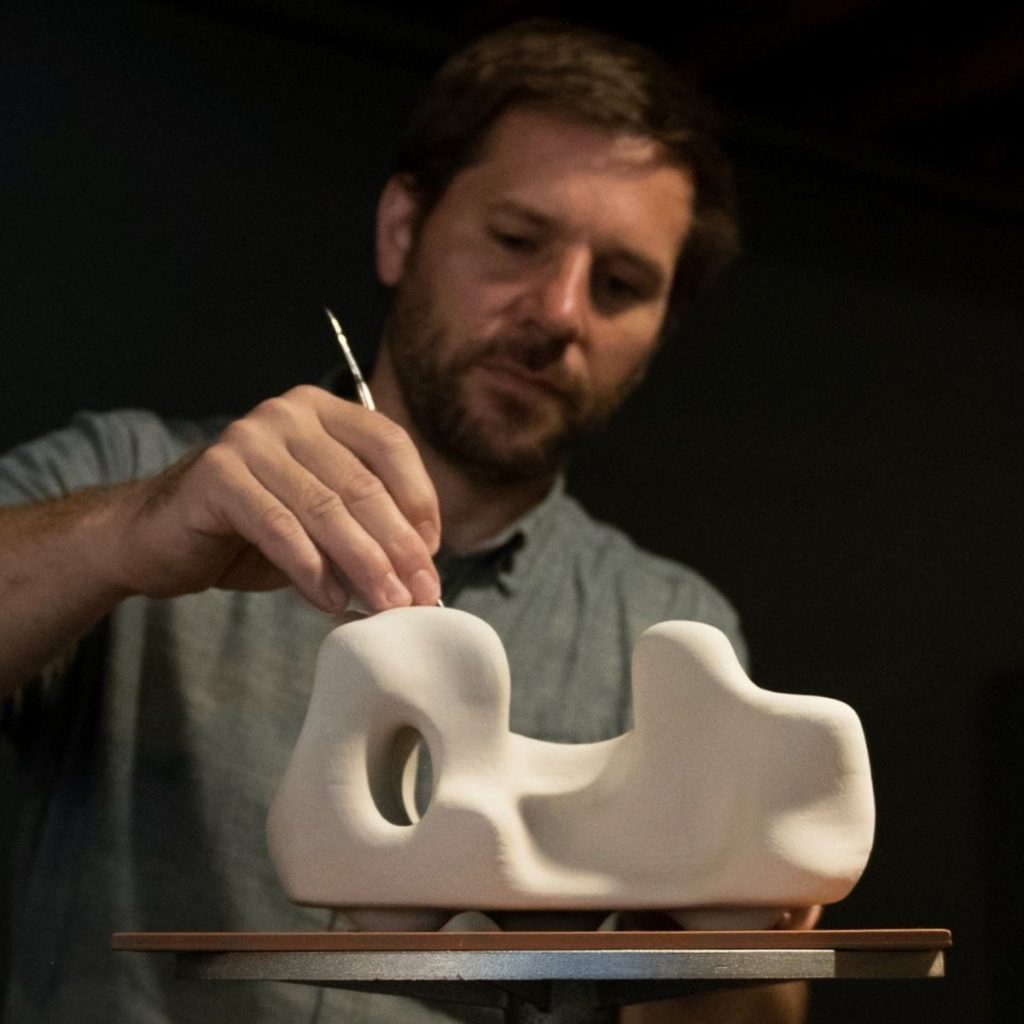
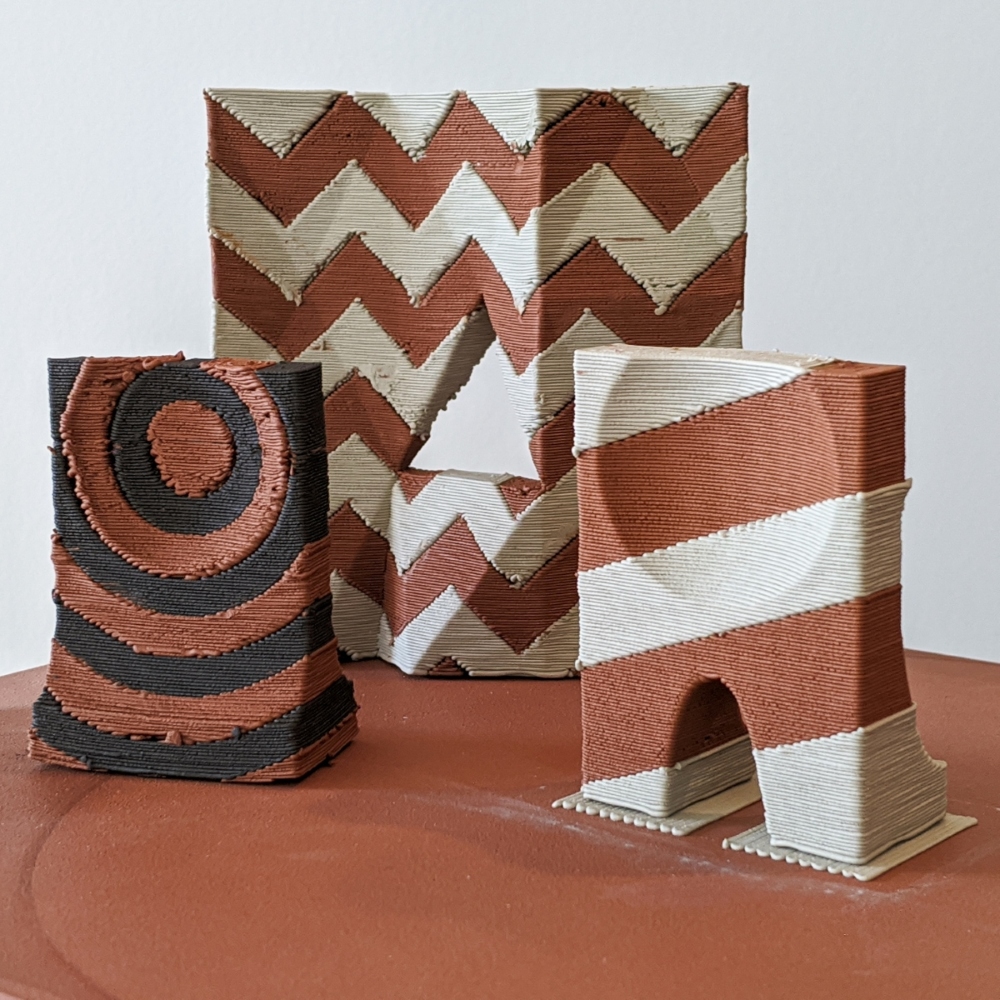
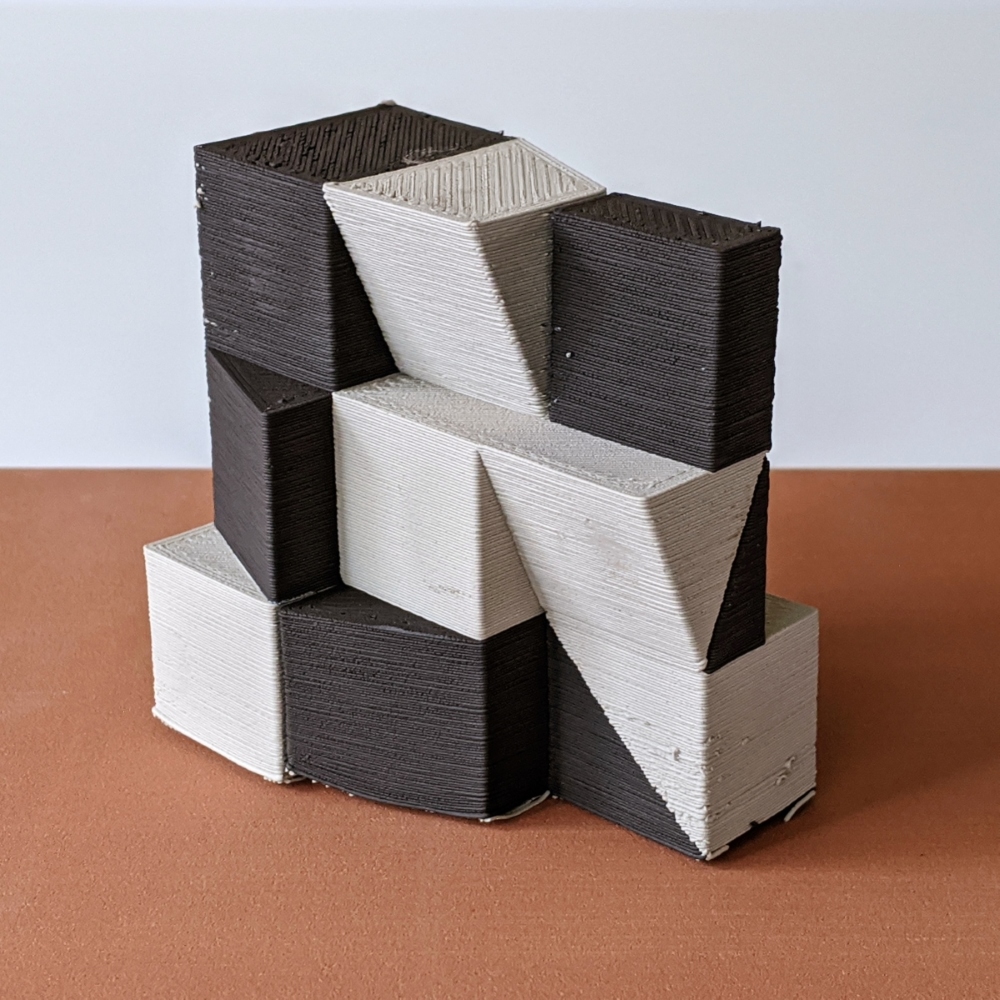
Tom Lauerman, an artist who also teaches at Penn State University, spent many years trying to perfect this technique. When he started experimenting, clay 3D printing was still very much in its infancy, and he was often criticized for trying to replicate a plastic printer. With his geometric clay sculptures often reflecting a degree of accuracy that, even now, is arduous to achieve, Tom Lauerman thought – “Why not?”. He commented that setting up and calibrating the dual extrusion clay 3D printer that he had built was a tedious and time-consuming process. Much attention needed to be paid to the challenges the overall design would produce – before it could be translated into a 3D model, ready for printing.
An artist who enjoys adding detail to 3D printed sculptural busts is Marlieke Wijnakker. She is the co-founder of VormVrij®, a company that designs and builds the LUTUM® range of clay 3D printers. After taking a 3D scan of a subject, it is converted into a 3D model that is printed in clay. Marlieke then hand sculpts and adds all the small details that the 3D printer was unable to achieve. Confronting to some, her sculptural busts are popular for those who do not want to sit for long periods of time, as one would usually do for a portrait.
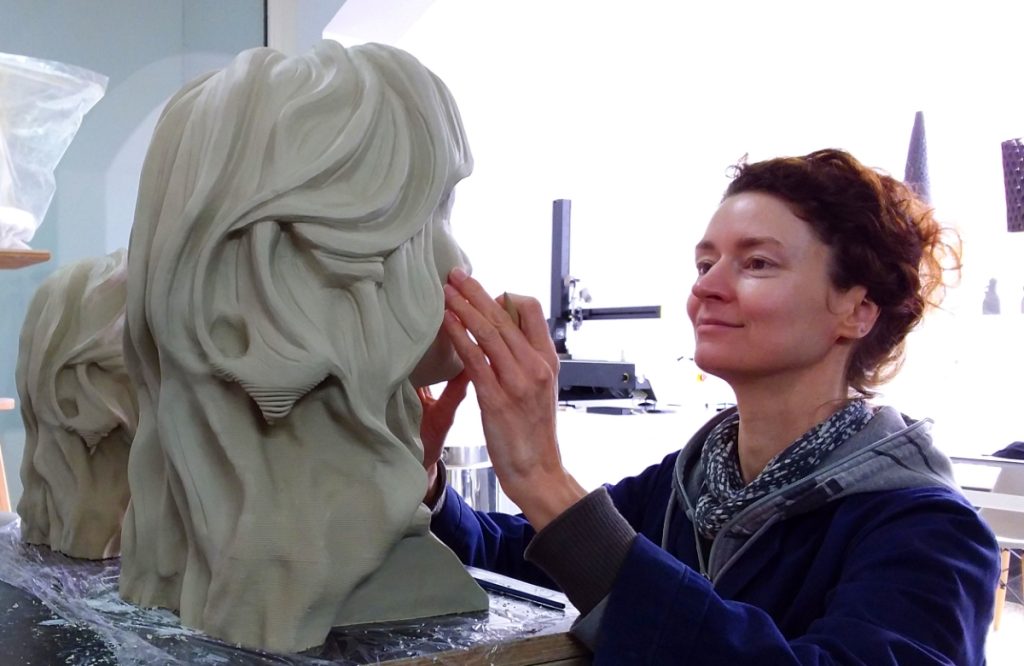

The importance of giving consideration to artists who move between different territories should not be overlooked… even if you do not necessarily agree with their techniques. The fact that they can apply these techniques should instead invoke questions. As a contemporary artist, this idea of “asking questions” has really helped me over the years to appreciate artwork by others who I would have previously skipped over.
Ryan Barrett is another potter who has also built his own ceramic 3D printer. Winner of the Great Pottery Throwdown in 2017, he creates jaw-dropping works that resemble colourful tapestries. Comprising over 10,000 clay coil layers, his love of textile design is reflected in his vibrant and colourful compositions. Glancing at his work, it almost feels familiar, but as you lean in and look closer, his intricate designs and attention to detail are revealed.
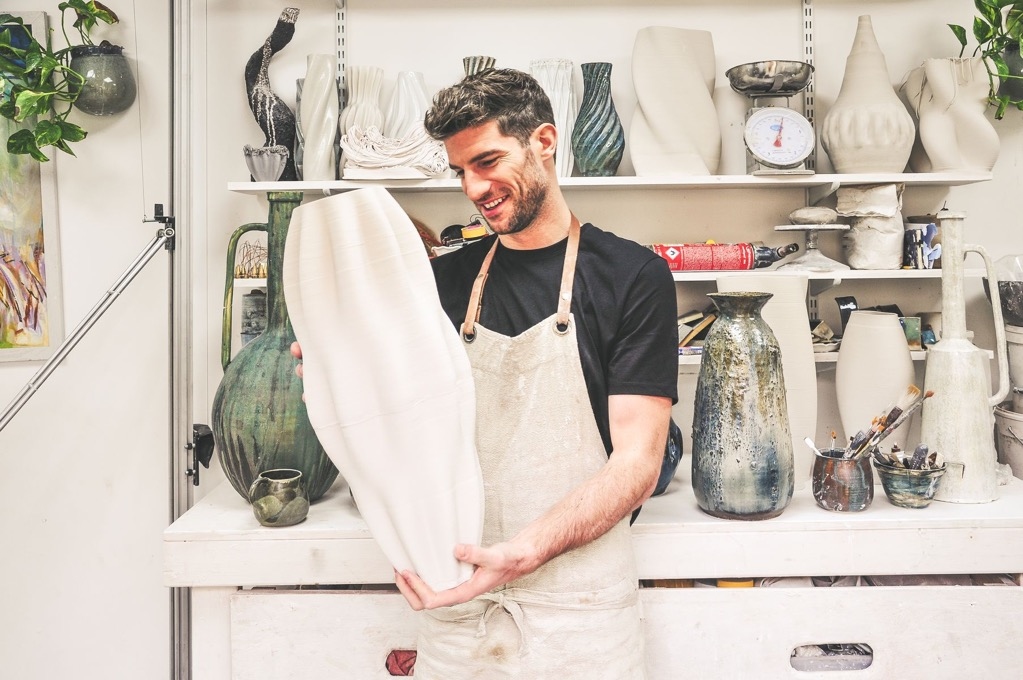
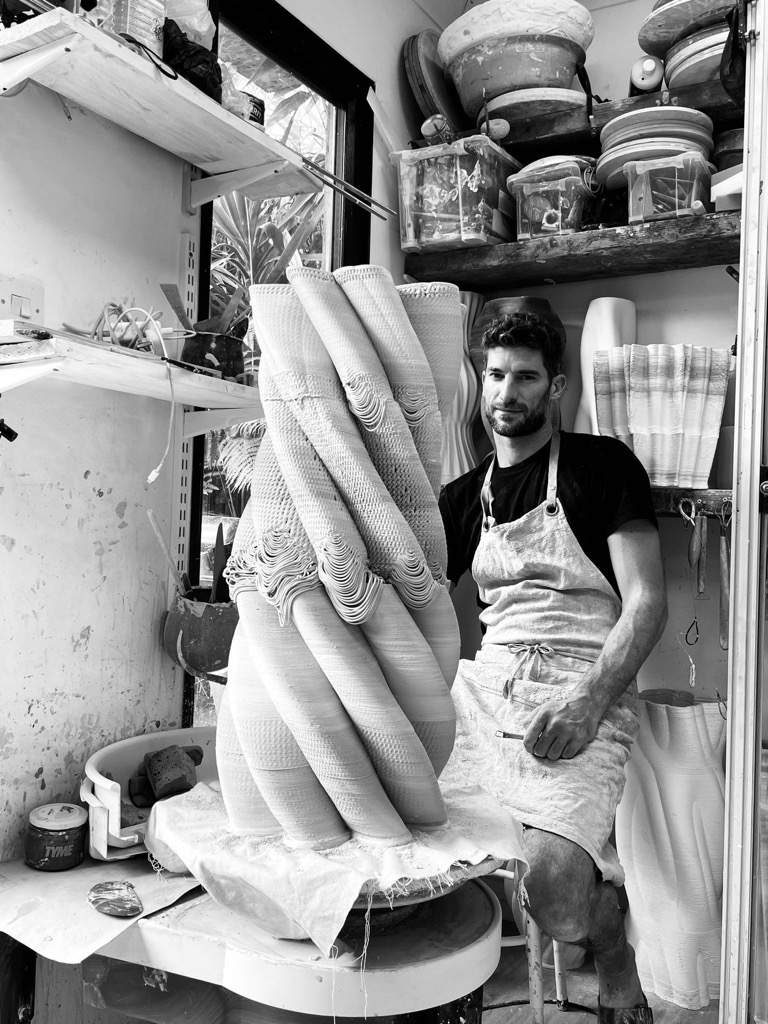
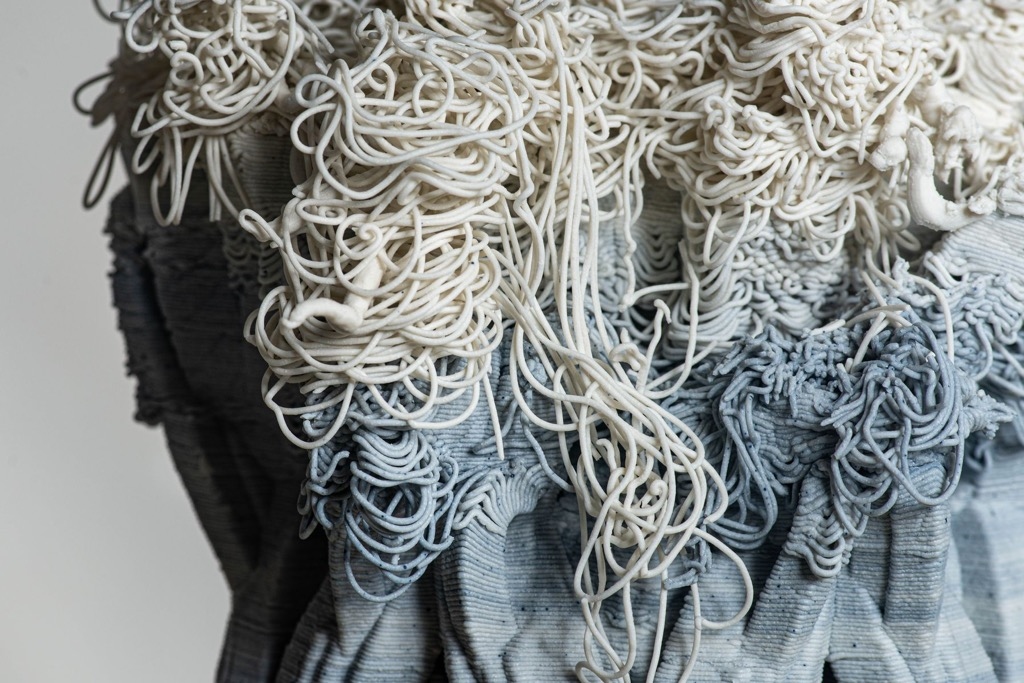
Design decisions should be intentional. Whether you are hand-crafting a sculpture or creating a 3D design in a computer software, you are actively and intentionally participating in the cultivation of an idea. My intention is not to necessarily persuade everyone that clay 3D printing is for them. Nor do I want to say that one pottery technique is essentially better than the other. Rather, I ask that it be considered before being disregarded straight off the bat.
Regardless of what your artistic process is as a potter, clay as a material can sometimes have a mind of its own, creating memories in the clay body as you work, with the kiln ultimately having the final say. A crack, a break or an explosion in the kiln is something all potters experience at some point, and if nothing else, maybe we can at least all agree on that!
Hendrien Horn is an award-winning artist and author. Hendrien is the first contemporary clay 3D printing artist in South Africa. She works from her pottery studio in Pretoria where she presents workshops. She has participated in numerous exhibitions across South Africa and received the prestigious Corobrik Award at the Ceramic Southern Africa National Competition in 2022. Her artwork, “Plutonic Form: Existing in the Abstract” forms part of the permanent exhibition at the Pretoria Art Museum.
Along with giving talks around the country, she has also created numerous online courses for beginner potters and 3D clay makers. Her book, “Let’s Clay 3D Print! A Guidebook,” was released on July 5th and features clay 3D printing artists and industry experts from around the world.
Ceramics Now is a reader-supported publication, and memberships enable us to produce high-quality content like this article. Become a member today and help us feature a wider range of voices, perspectives, and expertise in the ceramics community.
Photos courtesy of the artists.